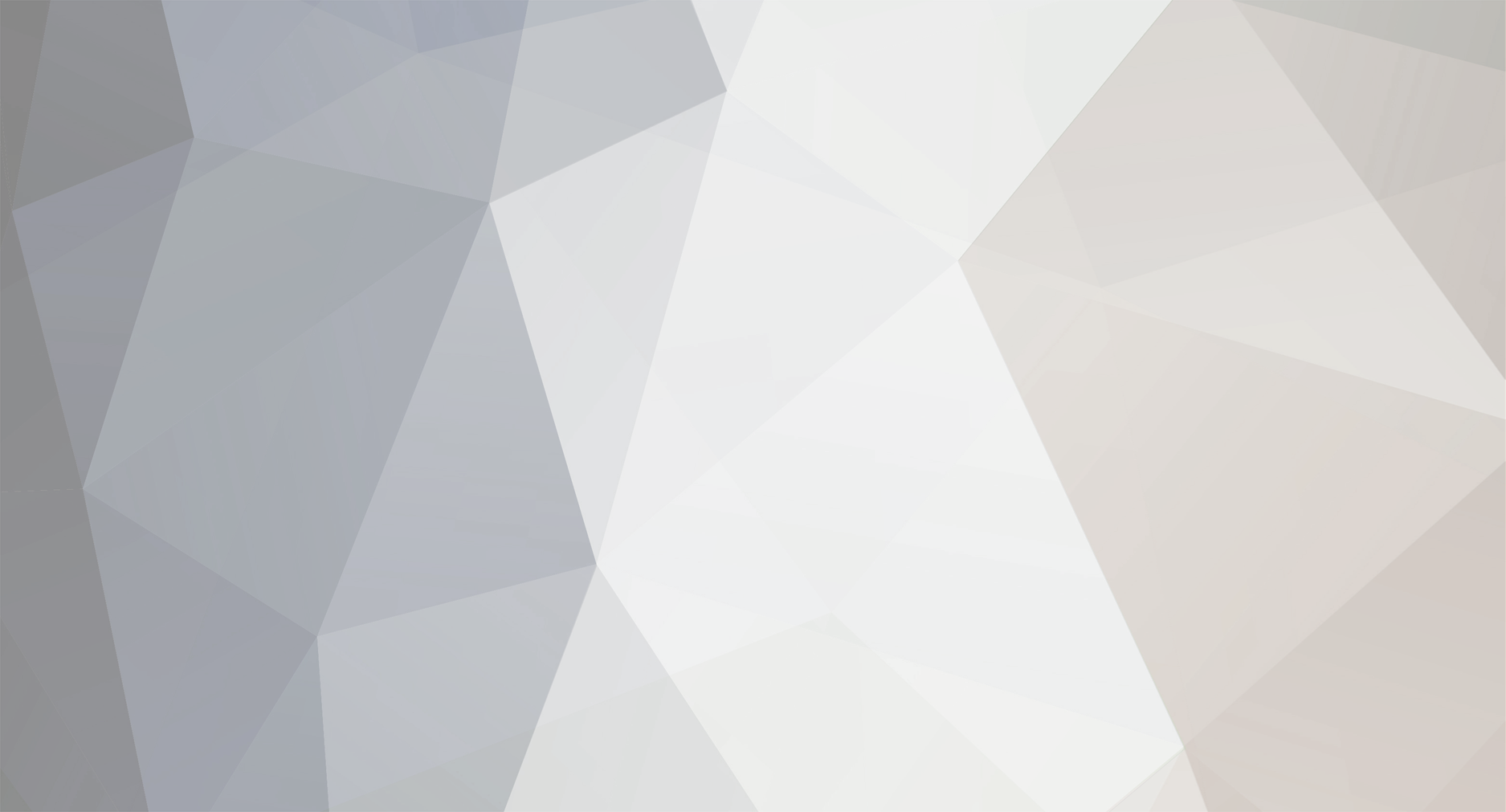
geezer
Member-
Posts
2,342 -
Joined
-
Last visited
-
Days Won
1
Content Type
Profiles
Knowledge Base
Zcar Wiki
Forums
Gallery
Events
Downloads
Store
Blogs
Collections
Classifieds
Everything posted by geezer
-
My first choice for removing as you describe "light overspray" is WD40 and one of those kitchen scrubbing pads, like a scotch brite but not as abrasive. Even get one out of the kitchen your already using if you want even less abrasiveness. I get no name brand ones at the dollar store. Follow up with a soap & water solution. Like E says, try the soap & water first though.
-
Zak: Is that the beautiful pristine early '71 dash you showed me at the swap meet last year? You haven't sold it yet? Alan: Your observations fit exactly with what I am familiar with. Right up to my retirement almost 8 years ago, the same type of overhead line, supporting a fixture was used to convey the instrument panels during their build. I have seen both the ones used by GM and Chrysler. They are the same design. I will try to describe them and how they work. The IP skeletons came from the Vendor in large racks holding more than a hundred, hanging lengthwise and nestled together. They were seperated by various protector strips which were removed and returned to the vendor for reuse. There were as many as a dozen different IPs so that made for a lot of racks taking up a lot of space. As I mentioned before, these IP lines were circular or oval. so once an IP was removed from the carrier jig and installed into a car it continued on and was reloaded with a new IP blank to be built. The carrier jigs consisted of no more than 2" square tube frames with locating pins at either end. There were 3 fixed camlock design hand clamps used to lock down the IPs. When loaded onto the carrier jig and clamped they were in the same natural, horizontal position, as if they were mounted in a car. On the ends of these square tube frames the fixtures were equipt with bearings so that the complete fixture and IP could be easily rotated while suspended by the uprights at either end. There was a spring tension cog & pin mechanism operated by a hand lever at one end, to release and lock into the desired position. This made it possible to place the IP safely in about a dozen positions on the horizontal axis for ease of assembly. In an overhead view you would see all these carriers in many different positions. So in conclusion, I can see how writing on the panels could be awkward and strained as it wasn't feasible to position the panel just for the purpose of writing on it. There could be someone else working on it while someone else is trying to write on it. I will comment on the steering columns later.
-
I can only generalize the use of these various markings. I am not knowledgable in the ways of Nissan. These cars were built long before the inception of ISO, so each manufacturer more or less had their own methods of verification. Basically, in an assembly operation such as the S30, where there are a number of model variances, vitually every part that had a counterpart for use in another market or every part that had an optional replacement for it, a method of ease of identification was nessesary. Picture a vehicle assembly line with work stations spaced along it. The stock needed for each and every possible build requirement was on hand. To aid in the proper part selection a variety of methods were used. It could be code stickers, paper tags, paint dabs, chalk marks, grease pencil, markers etc. Whatever method was used, it was meant to be highly visable and recognizable by all other workers stationed downstream from this operation. A mistake or wrong part installed doesn't usually get by without being noticed. Most of these markings came into the plant from the vendors. It was a design specification. This didn't address your question Chris but I thought it would help to point out some of the reasons for various markings. All auto assembly operations I have seen or have been a part of, used a method of marking the underbody/chassis components in a somewhat permanent manner. I have sandblasted my share of chassis components in my own restorations and some of these markings, paint dabs/slashes are still there after blasting. For the most part, other than part identification, the majority of underbody/chassis markings are used for torque verifications. I really don't recall any other reasons. All we can do is continue to share & compare what we find.
-
This photo and sketch are showing the Tram station. This is where the alignment is done by the man below in the pit. After the driver has positioned the vehicle and shut it off, the man below sets the caster & camber. Meanwhile the driver typically performs the headlight adjustments by aiming them at targets not seen in the photo. There is no better time to do this because the car is perfectly positioned. There were different targets/specs for different markets. This is true also for toe in/toe out adjustments, compensating for the crown in the road which is different depending what side of the road you are driving on.
-
After studying these photos I can explain what they are depicting, because it is not readilly apparent to someone not familiar with this equipment. The Rolls was an earlier/simpler version of a dynometer. Most of this apparatus is hidden below floor level. You cannot see the restraint device that rises up in front of the vehicle or the the exhaust reclaimation system. In this shot the car is not in position and the rollers are not elevated. They were double rollers that the wheels were cradled into. The yellow S30 was driven into position, and the rollers were elevated to the rear wheels, by the driver pushing the button and the test was begun. The vehicle was first placed into reverse gear and accelerated to 15 mph. It was braked to a full stop and then placed into forward gear (1st in the case of a manual) and then taken through the gears to 55mph. The braking was then tested again from this higher speed. I would like to point out the driver accessible red buttons in the photo. There is one on each side of the car (LH & RH drive). The rolls that we used here were very similar and had the same button system, using a single button to raise or lower the rollers. A very simple testing proceedure.This equipment has evolved over the years to nothing short of amazing, is computerized and capable of also testing All Wheel Drive, ABS systems, Cruise Control, Emission Control Systems etc.
-
Make that nine...you won't be able to sleep the night before she arrives...more anticipation than waiting for a mail order bride:love: She sure presents herself well in the photos with a "nobody's messed with me look", very pretty!
-
Hi Chris, The two sketches are new to me and way cool! I have to ask...is this your work? The overhead welding sketch is worthy of some careful study, as are all the other photos. The sketch of the car on the Tram is a familiar scene and very well done, but the headlights should be turned on. There just are not enough photos of these production areas, that I never tire of studying.
-
Mike: It's all guess work, unless we get some substantiation from someone who was employed with Nissan at the time, who actually spent some time on the shop floor and is familiar with the practices in this era. Arne: I would put my money on the VIN plates being already mounted before the IP was installed in the car. The windshield would not yet be in place. Even though other markets never had a VIN plate mounted to the dash, there was still a need to ensure the proper IP was installed because of the many variances. The build sheet would have accompanied the IP until it was mated with the corresponding car. A while back I shared some of my manufacturing experiences with a few members who had an interest in the processes employed in North America during this same time frame. The simularities with the practices in Japan are uncanny to say the least. If it wasn't for the language barrier, I would have been right at home in Japan building S30s. Here is an explanation of the stamps and their use here that I sent to Chris more than a year ago, because he collects them. Hi Chris, I followed a link yesterday that led to a discussion on stamps and their purpose. I didn't want to revive an old thread without pertinent information or a question pertaining to the subject. I thought since you are collecting them you would have an interest. I have experience with stamps in automobile manufacturing. I have attached pics with a few examples of stamps I have used. These were as much a part of my daily work apparel as my wristwatch. A correct procedure system was in place and all stamps were assigned and records were maintained on their possesion and use. They were issued to personel who were authorized to sign off on known defects or possible defects, that were either tested or repaired on vehicles in the system (those would relate to the Ken stamps), or parts OK'd to re-enter the system after being reworked. Re-work is a separate department with a team of very busy, multi talented people, who daily, anyalize and come up with solutions for a multitude of problem parts coming from the suppliers. These are stop gap measures to keep the line rolling until the supplier has the problem rectified. Some suppliers had their own buyoff stamps that were used also to identify and sometimes date their re-worked pieces. (I believe the stamp in question in the thread was a rework stamp. I couldn't say if is a supplier stamp or used internaly though). There were quite a variety of stamps. When I was the Production Co-ordinator for the Windsor Assembly plant, I was charged with ordering, issuing, recording and tracking the use of these stamps. The design of them progressed over the years. The circle was incorporated into the design to improve the quality/readability as it is slightly raised and lessened the chance of the image being smeared. The one on the far left is the first one I was issued in the late 60's. Because they are ordered in bulk I actual used one that was original issued to someone who had died years before, but it was registered to me. Just a tidbit, Ron
-
Graffiti was mentioned as a possibility for some of these writings, but in all honesty, I think there were legitimate reasons for these particular ones portrayed in this thread. I will pass on my thoughts at the risk of over speculating. Doing so may allow someone who is translating the writings to put 2 and 2 together and bolster their own theory. The markings being discussed in this thread could possibly serve more than one purpose. The instrument panels would have been assembled on a separate line (probably circular) and meet up with the trim line when completed. With all the different market variants there would be a need to schedule the panels to be sure each car meets up and meshes with the corresponding correct panel, complete with the VIN tag attached. It would be the panel installer’s responsibility to make sure the VIN on the panel matches the build sheet accompanying the car. Because of these examples of HLS30s having such a variety of markings on them, even if there is no discernable difference in the build, we can rule out the likelihood of the bare panel coming from the supplier with this writing. The panels would most definitely had build sheets with all the necessary information, travel with them while being assembled. So, no writing required yet. I don’t know for sure how many different steering column assemblies there would have been for all markets of the S30 in a given time period, but I’m guessing 3 or 4. Could the markings possibly indicate what steering column assembly was called for? I don’t think so, simply because I can’t think of a reason to mix numbers with these other writings. (By the way, my IP only has the number 46 written in this location.) I’m guessing an approximate number of people needed to man this instrument panel line to be about 20, with one of them being a repairman who would correct any mistakes in the build or change out parts for whatever reason. With maybe as many as 30 carriers, each with an instrument panel clamped on them, suspended from this circular line, the repairman would be free to perform his work on one panel and then move to the next one that requires work. How would he know what work was needed without running the risk of missing anything or needing to visually inspect everything? The assembly workers on this line possibly wrote on this area to give the repairman the “heads up� The two digit numbers could be the callout numbers for a particular part listed on the build sheet and the other writings could be symbolizing other repairs. (I would love to see a build sheet.) Or… As the demand for these cars intensified measures had to be taken to maximize productivity. One of the most popular and effective ways to do this is, eliminate the need to shut down the assembly lines for contractual breaks. By using relief men to take the place of workers taking their break a great many more cars can be built in the course of a day/week/month/year. Some of these jobs would carry a great deal of responsibility to not make a mistake and the consequences of causing the main line going down would be dire. This is why a method of marking their work was devised by most relief men when taking someone’s place while they were on a break. A screw-up could be traced to the one responsible. Too many times the words…it must have been the relief man, had saved someone’s arse and cooked another. Typically, the relief man would mark the first job he worked on and that’s it because he would replace the worker for a set number of jobs/units and since they are scheduled that’s all that was needed. These are just a few points that came to mind while reading this thread. Take it for what it’s worth; it comes from my 33 years at almost a dozen different auto assembly facilities, working for 3 different manufacturers and an over active imagination.:classic:
-
Bob, all the stampings I recieved from Mill Supply came complete with Tabco stickers on them. I was told by the fellow taking the phone order that the parts were made by Tabco and they were having difficulty getting certain stampings...hence the long wait. I don't think Mill Supply does any manufacturing. I may be wrong but I think they only operate a retail outlet. All I can say is, prepare for a bit of a wait for at least some of these parts.
-
Thanks for the tranlations. After finding the meanings of these writings, I would be inclined to agree wholeheartedly with the above quote. I have seen all manner of self expression displayed on vehicles built in the US & Canada and see no reason why the same didn't occur in Japan. Everything from "Have a Nice Day" to "Built by White Punks on Dope". We even found an over zealous inspector who took it upon himself to make notations in the owners manuals warning of potential problems that may be experienced in the future. In the '60s & '70s it was common for painters to initial parts such as hoods & fenders and the vehicles themselves with the gun (in an inconspicuous place. Interesting nontheless.
-
After many failed attempts to buy stampings from Tabco direct, I was left no alternative but to deal with Mill Supply. Only downside I suppose was slightly higher prices. This turned into a waiting game because all Z stampings sold by Mill Supply are produced by Tabco. It was more than 6 months before I recieved email confirmation of the parts availability. Don't get me wrong...I am grateful someone is still punching out these pieces, even if they leave a lot to be desired. I would not recommend that someone without metal working experience attempt to fit these parts. They are close but lack the superior sharpness of definition that you get from genuine Nissan stampings. Regardless of who the end supplier is, I believe Tabco is the only outfit producing the stampings today. Bob, that explains alot. A move to a new facility would have put Tabco behind schedule and caused me a 6 month wait. Anyhow, the parts are usable and the only game in town, unless you can track down NOS. Thanks for the report on your tour, it is always interesting to get the perspective of someone who has seen it first hand.
-
-
Yes, the 1972 HLS30 started at serial number HLS30-46001. The beginning serial number for the change to the horizontal defroster grid was HLS30-062001.
-
JUANZ, this was just listed on Ebay. http://cgi.ebay.com/ebaymotors/240z-260z-280z-hatch-panel-very-nice_W0QQitemZ180268378503QQcmdZViewItem?hash=item180268378503&_trksid=p3286.m14.l1318
-
Yes, the Canadian models had a separate designation. After Jan 1970 all US market cars were mandated by law to have a fuel vapor recovery system and were also equipt with an air pump. Not so in Canada and also the fuel tanks continued to be vented to the atmosphere. Also, a higher amperage battery along with a higher output alternator were incorporated into the Canadian models to better cope with extreem cold. Other differences escape me. I found it interesting how many different model designations there are. While doing some other research I came across a chart that shows the 36 different model designations for the North American market in the transition years of '74-'75. I have never seen a listing of model designations that includes all markets worldwide or a breakdown of the significance of each, but it would be quite an undertaking to lay all that information out. When these cars were built, the cars were accompanied with a build sheet that included the Model designation. This told the assembly workers what components were called for. Different models were needed to comply with mandates imposed by the various countries and also differences developed by Nissan. I'm of the opinion that all models destined for all markets were intermixed and run down the same assembly lines for the most part. Back to the pamplet. I imagine the lead time was substantially longer than today to get this printed material developed and off to press. Also, many final decisions and changes to the final product were probably made but not reflected in print. It's all part of what makes the early cars so interesting.
-
Congrats! We know you have been patiently waiting for a good deal to come along and lets keep our fingers crossed. Most of us North of the border know what it is like to buy with only the pictures provided by the seller to go by. Sure does look pretty in the pictures, but you know they all "need a little work"...famous last words. Gonna be a long 4 weeks. How are you getting it home?
-
I really enjoyed reading your post. It seems to me you have aproached the evaluation & assessment in a most sensible manner and prioratized the maintainance schedule. The former owner can take comfort in that this beauty is in capable, appreciative hands. Safety and reliability are foremost, everything else just widens the smile on your face. We hear so many horror stories, it is refreshing to hear one with a happy ending once in a while.
-
That picture Stephen put up isn't too bad. I used this link to a monitor cleaner that cleans the inside surface well. http://ezfolk.com/screenclean.swf
-
If you start saving your coins now, by the time you go to Japan you might be able to afford this system by Fujitsubo, in stainless I believe. Notice the similarity in design of the header. Also in the 3rd & 4th pics the header shown is actually stamped L20. This makes me wonder how many different headers were produced in a similar design with maybe minor differences such as tube diameter or consideration for installation on different engines, in different models, or even a LHD. If I was a betting man, I would bet the one labeled L20, #14004-E4620 and the one I have were all produced by the same manufacturer. There does not seem to be much interest in these 30 plus year old exhaust systems, because of the extra weight of them and perhaps the better performance of the newer designs on the market. Thanks for the offer of picking up a binocular gasket for me. I would appreciate it and will gladly reimburse you. One suggestion...before going to Japan take some measurements and make a template to gauge steering shaft clearance. If you need help doing that I can explain how it's done.
-
That could be quite feasible as they would be able to be stacked together easily.
-
The paint looks great! In the pics it looks a lot like 901 silver. Glad to see another Z being recomissioned. Good stuff Jim!
-
How difficult it is to put a 280Z F.I engine in a 72??
geezer replied to guy_geo's topic in Engine & Drivetrain
"snap" ...just a figure of speech, meaning easy. I think Bruce means it is easy to put the EFI engine in...making it run as designed, much more difficult, time consuming and costly. -
ainokoz - It is a good thing we left 5% wiggle room here. The header in the pic you put up is indeed Nissan part #14004-E4620, I believe. My header is a Trust and different then yours. Confusing to be sure, if you don't have both images along side each other to compare. If you look at one, then turn and look at the other, it is so easy to mistake them as being the same. Take a look at the 4th tube from the front on your pic or the illustration in the Sports Option pic. See how this tube tucks in behind the 5th & 6th tubes. Now look at mine. The 4th tube from the front enters the collector moreso oriented to the front. I think that is the easiest eay to tell the difference. It is not noticeable without careful study. So to sum up my opinion, mine I believe is a Trust and will fit on a LHD. The one in your pic is #14004-E4620. I still don't know if it will fit in a LHD. The last time I researched this I found the one in your pic much more common and easy to find, whereas the one I have is more unique. I have never seen another like it yet. Not even a pic.