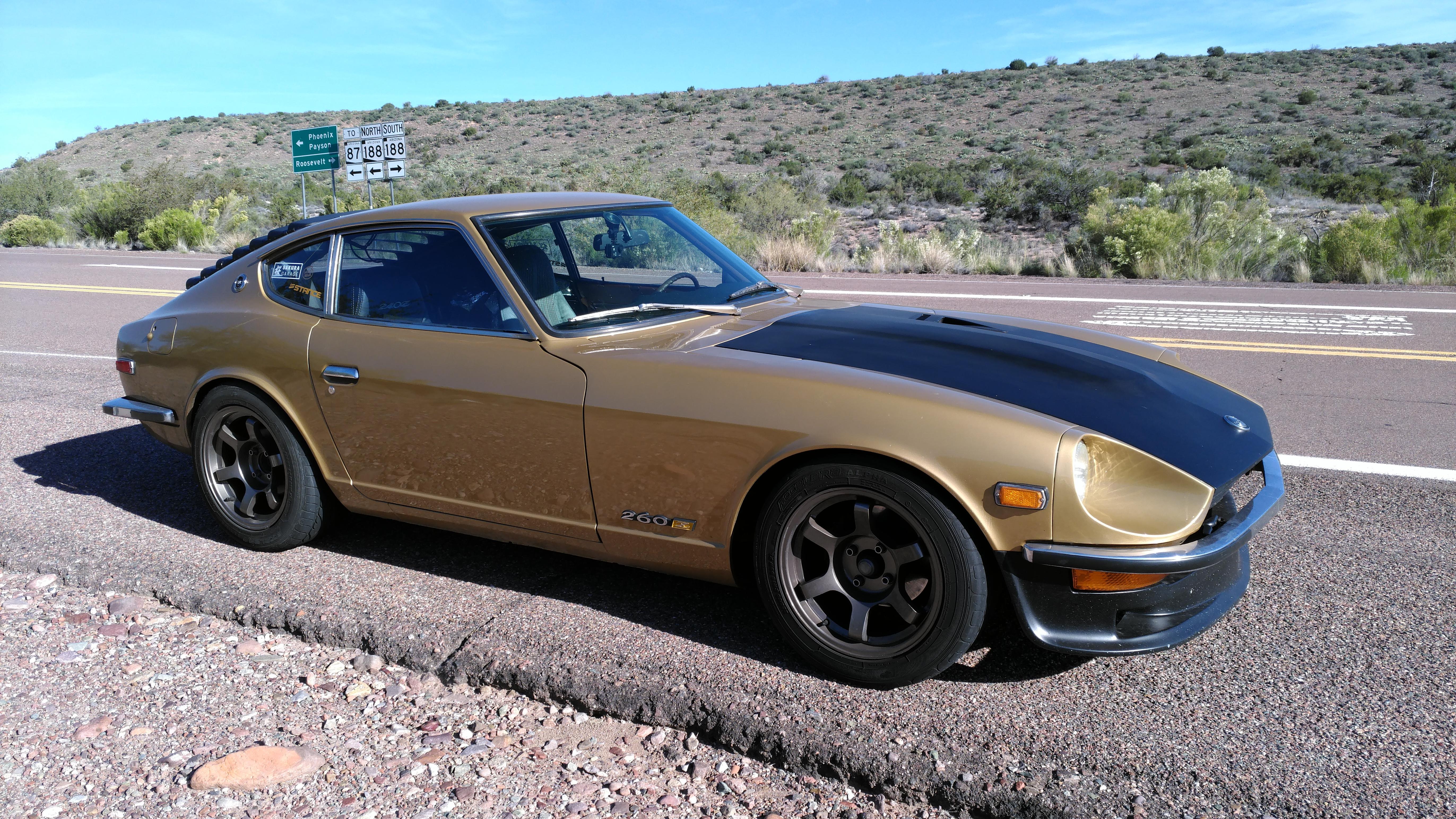
Everything posted by cgsheen1
-
Assessing Manual Transmission Condition
That's what's in my close ratio right now. Although many have reported good results with Redline, it didn't work well in mine. IDK why. I'm going to try the Delco Friction Modified gear oil next change.
-
Steering wheel parts
It holds the padded horn "button" in place.
-
Parts Wanted: 1977 Datsun 280z Clock Wanted
If you're still looking, I'll go through my stash. I have a few working clocks but I think they're mostly from earlies. '77-'78 are pretty rare here. I do have a working original '78 Quartz clock but I don't know that I want to give that up...
-
1972 Z intake manifold smog plug sizes
I'm blinded...
-
Assessing Manual Transmission Condition
That's correct - and the shift lever has a spring and different bushings than the early transmissions.
-
Bright Links On Timing Chain - Line Up Every 11 Rotations
11 bothered me because it's not an even number. 11 turns of the crank turns the cam 5.5 turns, right? How can the dot line up with the link other than on a full turn? 110 chain links / 40 teeth on the cam = 2.75 cam revolutions for one complete chain revolution. 2 complete chain revolutions = 5.5 cam revolutions. 4 chain revolutions = 11 cam revolutions. 11 cam revolutions = 22 crank revolutions. 11 cam revolutions * 40 teeth = 440. 22 crank revolutions * 20 teeth = 440. 440 is the first number we can get to that is evenly divisible by 110 chain link holes, 20 crank teeth, and 40 cam teeth - isn't it? (110, 220, 330, 440) Somebody check my math - and logic... (11 cam revolutions bothers me - because it isn't even.)
-
75 280Z won't run.
What?? And that makes sense to you why?
- Duffy's 1/71 Series 1 240z build
- Duffy's 1/71 Series 1 240z build
-
75 280Z won't run.
You certainly don't...
-
75 280Z won't run.
It certainly is. Bunny Ears... (ish)
-
Duffy's 1/71 Series 1 240z build
Well, any crank wheel is enough to run it all, but how... What madkaw is getting at is this: The crank travels two complete rotations to complete one engine cycle of "four strokes". Top Dead Center occurs two different times during the complete engine cycle. With a toothed wheel attached to it, the crank can "tell" you when TDC has been reached BUT it can't actually determine if it's on the compression stroke or the exhaust stroke. (no matter how many teeth you have, or lose...) Usually we go to the Cam for that information - it runs at half the crank speed. Since the Cam only makes one rotation for every two crank rotations, a separate sensor on it can tell you when TDC is on the compression stroke - and that's what we're most interested in. Those of us running full sequential ignition with most aftermarket ECU's need input from both the crank and the cam to provide the exact engine position needed. There are other methods I'm sure, but those are most common. Using just the crank toothed wheel input, I could still run individual coils (COP) in a "wasted spark" mode - and the Haltech ECU is certainly capable of doing that. Wasted spark fires two spark plugs at the same time on opposing cylinders so it doesn't really matter the crank position. It's firing cylinder one at both TDC compression and TDC exhaust - it can't "get it wrong". (How could it "get it wrong"? The engine doesn't stop at the same place every time. When you shut it off, the ECU can't keep track of it's exact location and "know" it's exact position when you start it back up again - that's why they need position sensors...) IF Haltech can glean enough information from a toothed wheel (not using a cam sensor input) to run full sequential (not wasted spark), I think there are many that would like to know how they do it. (BTW, I can't see how the Hoke toothed wheel is 60-2... On the linked site it shows his as a typical 36-1. Not that the number of teeth makes any difference. More teeth normally just means better resolution but more teeth can also be harder to "read" accurately at high RPM - so they strike a balance when they invent these things.)
-
vintage dashes 280z
? Ya, I noticed that after I reinstalled the speedo a few weeks ago. I've just been too lazy to get back under there to change that lower right bulb... I don't do much night time 140mph driving anyway. I mostly use that left side of the speedo. You guys may have shamed me into doing it before October though.
-
vintage dashes 280z
Yes, stock 3.4 watt bulbs, green plastic domes all cleaned, and repainted inside the cans with flat white. The lower right bulb in my speedo is not working. I just haven't gotten under there to replace it... Too hot in Phoenix. The speedo is the latest gauge to get new white paint inside though. In my gauges, the original paint inside was kinda minimal besides being discolored. I generally covered the entire inside or as much as I could do with flat white. Flat also seems to make the light disperse a bit more. Repainting seems to make the biggest difference.
-
vintage dashes 280z
While you have those gauges apart you should pull the guts and repaint the insides of the cans a nice bright flat white. No matter what bulbs you choose, that will always help. Personally I don't like the harshness of the LED replacement "bulbs" that I have seen - I'm very old school that way. But repainting the inside of my gauges made a huge change in the brightness even using stock 3.4 watt bulbs.
-
Can't align HVAC trim panel?
Are your mounting tabs behind the faceplate out of alignment? The "lever panel" in the 260/280 is fixed fairly stoutly left-to-right (though it moves up and down). The finisher shouldn't press up tight to the HVAC panel - there should always be a small gap there. Mine fits fine(ish) and I've never had any interference with any of the switches or levers. After going out to take this picture (of my dirty vents) I'm struggling to understand why moving the finisher would cause your fan switch position to move... Are your lower levers resting (scraping) on the finisher? Mine is off-center too - maybe not as much as yours. Wow, I need to clean...
-
Water in the foot well.
Ya, sounds like A/C condensate...
-
Rear Spindle Pin
Yup. I've been lucky with most of the spindle pins I've had to remove but I've had three or four that had to be cut and the remnants pressed out. There's one thing I've noticed about many of the spindles I've extracted: The metal is relatively soft and is "mushroomed" at the edge(s) of the Lock Bolt chamfer easily by improper installation of the Lock Bolt. I've pulled quite a few that were not locked due to corrosion but were difficult to move because of the "swelling" near the Lock Bolt. I've generally found that if I can rotate the spindle, I can usually knock it out with a drift - even if it's mushroomed. Always put your Lock Bolts in correctly and torque them properly to avoid this type of damage to the middle of the spindle.
-
300hp out of L28 non turbo
Ding ding ding. I've driven a 300WHP 240Z without chassis modification. (RB swap) It was stoooopid fast - scary fast. Not that you can't drive it that way BUT it twisted the hell out of the chassis. Popped a bunch of the spot welds in the rear - creaked like a Spanish Galleon. The owner had to find another frame to put the drivetrain in. On the other hand, my sons '76 280Z (L28ET) makes 230WHP and 280 ft/lbs of torque, runs nice, is FAST, and doesn't tear the hell out of the frame... If you're going to put HP in a 240Z, LOOK TO THE FRAME.
-
Air ducting for 280z
Yup, that's it. Now you just need a small duct to run to the vent outlet under the steering wheel!
-
Parts Wanted: Roof with Pillars (no Sunroof) or possibly roof skin
Ever drive to Phoenix? I have a roof skin down here. (and rturbo is exactly correct - you need to de-skin the sunroof. The pillars are multiple pieces of folded metal. The skin has lots of spot welds but not nearly as bad a job as I first imagined. Plus,` body lead at the four corners - melt it out and wipe it off. We've done a couple here at the shop.)
-
Putting A/C back together 78 280z
The early Z's did not have a low pressure switch - those didn't come until the ZX. The Pressure Switch on the '74-'78 is for high pressure. You should be able to substitute a generic (universal) High Pressure Switch and the thread on those is pretty standard. Just a little rewiring of the connection. That's too bad about the little filter - you need the brass part to make the flare work.
-
Tips/tricks for removing windshield
I used to use thin stuff like that. Until I tried 1/4" cotton cord - wet. I've done 3 or 4 that way now and it works so much better, pulls so much faster, no torn rubber, faster around the top corners, it amazes me. Ya, this stuff - wet - it's unbelievable.
-
Putting A/C back together 78 280z
Picture of your receiver/dryer? They sell a cleaning fluid for A/C systems at the auto parts store - read the usage instructions and see if that's something you're interested in doing. I've run 134a in my stock A/C system since I put this car back on the road 9 years ago. To convert, get as much of the mineral oil out of the system as you can. Replace it with ESTER OIL not PAG (unless you can completely remove the mineral oil from the entire system). I use Ester Oil in mine and it works well. If you have a stock blower, replace it with the KIA Sportage blower - search, you'll find a KIA blower upgrade thread. Many people don't do flare fittings correctly. Make sure that all the mating surfaces are clean. Don't over tighten. Use a little refrigerant oil on the mating surfaces and on the back side of the tube flare (where the nut will cinch up). Snug the fitting - don't over-tighten. (When you over-tighten a copper flare, the heat causes micro-fractures = leak. Better to under-tighten, test joint with soapy solution after you pressurize, tighten more if necessary.) (last time I replaced my receiver/dryer I could get a stock one. I bought a universal and a ZX - either will work with some manipulation (of the bracket and/or the tubing). The nice thing about copper refrigeration tubing is that it bends (and flares). You can bend the tubing to fit if necessary - you can even make a completely new tube - it's standard 3/8" refrigeration tubing on the liquid (high pressure) side. The receiver/dryer I got has standard ports for the high pressure switch to be screwed in.)
-
77-78 map light
Exactly what mine does. But then it's 45 years old and rarely if ever gets used. I would imagine there's a brass contact in there that could use a bit of cleaning (de-oxidation)... I've never been motivated enough to see if that cracks open.