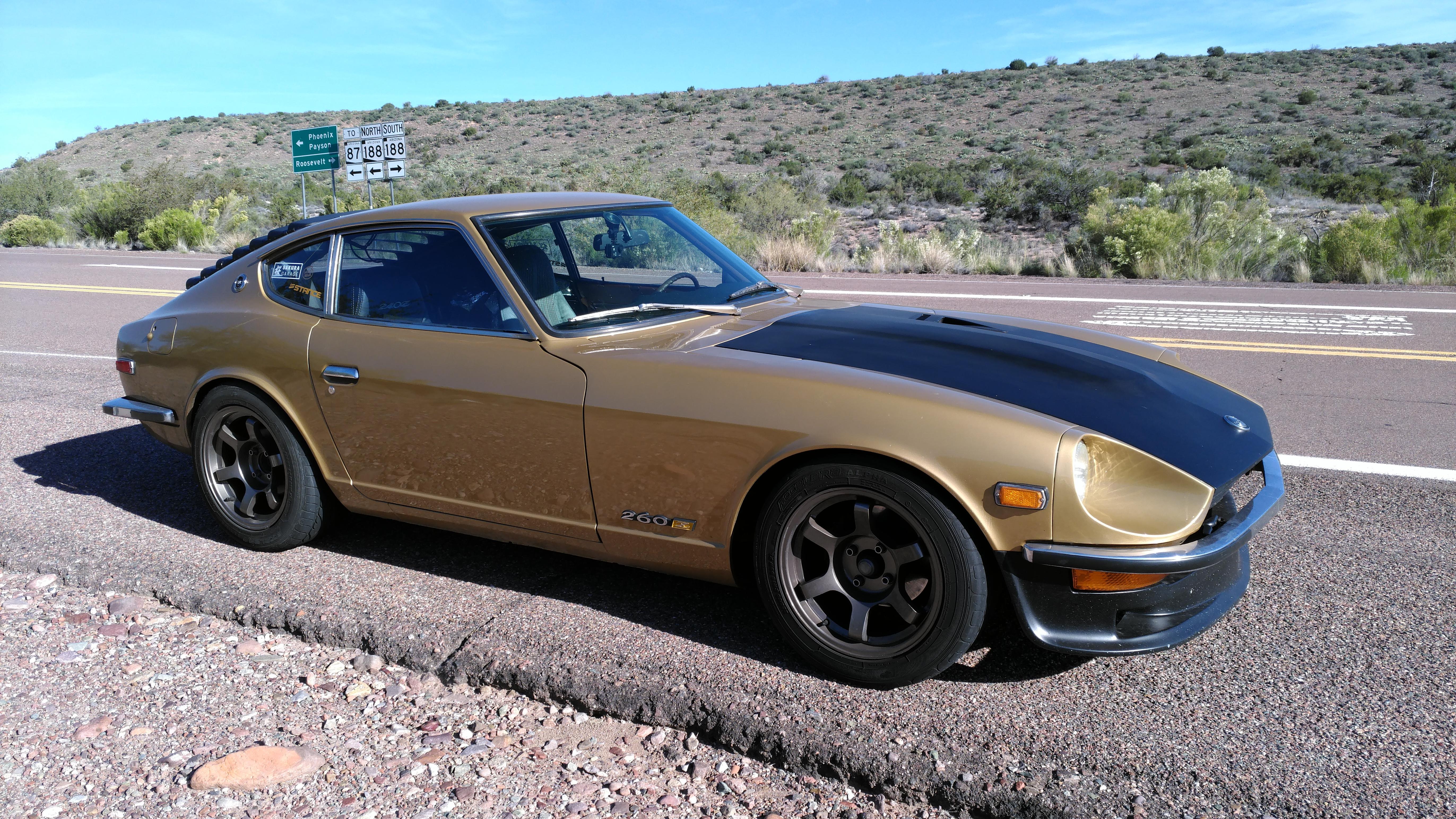
Everything posted by cgsheen1
-
Advice for inertia kill switch
Either way you break the circuit and stop the pump if the inertia switch is tripped.
-
LED Headlight conversions - My Recent take
Yup, bought those in Feb 2020 for my H4 housings and love them.
-
Rear Diff.
I ran the stock R180 3.36 behind my L28ET for years before my kids shamed (badgered) me into swapping to an R200. Personally, both me and my turbo motor were just fine with the R180 but it made the kids happy for some reason... You NEED an R200 = Internet Wisdom.
-
Guidance: installing A/C into 280Z
If you pulled the compressor back there and didn't seal up the hardlines to the evaporator, chances are the expansion valve components inside have rusted and it may be Borked. Here there's a much less chance of that happening. You might see if you can push A/C cleaner through the liquid line (at the firewall?) and catch what comes out the suction line in a rag. If your expansion valve is OK I'd say it's definitely worth keeping. It's pretty easy to flush all the other parts. Get a new Sanden, have a couple of hoses made for the compressor conversion, replace the dryer, charge with 134a...
-
Guidance: installing A/C into 280Z
Semi-interesting that they say it's for Lates (74-78) but their pics show a 240Z dash and center section controls...
-
Guidance: installing A/C into 280Z
Not opinion - that's fact. And while I prefer keeping the A/C in these things as stock as I can, there are very few of us that can deal with all of the oddities. I've been toying with the idea of building a more stock-like A/C system for both Lates (74-78) and Earlies (240Z (the Japanese S30 had A/C as an option)) using new and more easily obtainable parts. Maybe someday...
-
vintage dashes 280z
I'm with you there! I got my drivers license in the mid-60's and I'm used to INCANDESCENT GREEN gauge lighting - it's my preference. That is the very reason I originally kept incandescent bulbs in the gauges and developed the cleaning and painting method I've used for years on gauge bodies to maximize the output of the stock lighting. I had a customer several years ago that bought some of the first LED "bayonet" bulbs and had me install them - I hated the brassy-ness of the light... They were bare LEDs (no dome). I finally gave in after I replaced my H4 headlight elements with LED replacements. Then I wanted LED replacement bulbs for my turn signals and marker lights to reduce the amp load on that lighting circuitry... Then I decided to try the occluded dome gauge lights that I bought thinking they might diffuse the harsh light enough for me to live with. I still don't LOVE their light "temperature" but it doesn't bother me that much and they are (or can be) so much brighter than stock. That helps me quite a bit with the Phoenix light pollution on our streets and freeways AND I can adjust them DOWN when I'm traveling out of the city.
-
75 280Z Leakage from top of gas tank when filling
We've had a couple of fuel tanks with leaks on the solder joints at the hose fittings so you can't totally discount that. Hoses are more likely. Dropping the tank is fairly easy even with the myriad of hoses. Just disconnect the ones you can see and bring it down slowly until you can get to all of them.
-
Replacement Windshield Options
We have never broken one during removal or install. We were very nervous about removing and reinstalling the windshield with the crack so we were super careful (and had a fair amount of experience on our side at that point.) In the beginning, we were super careful because we weren't sure we could find a replacement. Then we had some solid experience, and had developed a removal method once we found that we could source replacements. I have broken a windshield out of the car... On our shop move a few years ago, I didn't pack one well enough... And, who says it doesn't get cold in Arizona? Why I've seen temps in the mid-to-upper 30's!! - well, until the sun comes up... (and I'm wearing a light jacket while these Arizonan's are bundled up in ski parkas - I grew up in Idaho and waited for the school bus in -30 temps.) Okay, I'll admit that we don't trust any modern windshield installers. They glue windshields in. That's pretty much all they know. A gasketed windshield installed over a flange is foreign to them. So, here's how we don't crack windshields: A. Use a utility knife (Xacto knife, single edge razor blade) to slice away the thin rubber that holds the trim on. Remove the stainless steel trim. 2. Utility knife - slice the exterior gasket carefully in the flat that was covered by the trim. You're looking for the edge of the glass. Once you find it, cut around it - all the way - enough that you can remove all the rubber from the outside face of the glass. 2b. You can do the above by yourself, but what follows really needs an assistant. Or two. c. Carefully push the glass out from inside the car. Lift just a little bit all along the perimeter until you're sure that all edges of the glass are unattached and it can be removed without interference. D. Remove the rest of the original gasket from the flange and clean the flange completely. REMOVE the dash finisher (the black crescent moon shape metal piece). 5. Get the new or exisiting windshield on a stand and install the new gasket on the glass. Be sure the glass is fully in the channel all around. Lube helps - very soapy water. 6. Install the stainless steel trim - not the corners, just the long pieces. Ya, do it now - it's MUCH easier than after the windshield is in place. The back side of the trim IS SHARP. It'll slice the rubber if you're not careful. You can file or sand the sharp edges if you're OCD (or even if you're not...) You have to raise the rubber flap up and over the edge of the trim. Lube helps - we use Meguiar's Hyper Dressing - and a smooth skinny tool: Awl, pick, screwdriver, smooth without sharp anything that will cut the thin flaps that hold the trim. g. Install a long cord in the gasket groove - thicker is better - like the olde tyme clothes line cord, cotton is better, but I have 3/8" polyester that works. WET the cord FIRST - yup, soak it in water. Add a little dish soap if you want, we need lubrication. The cord needs to pass each other at the meeting point by 10-12 inches. We like the meeting point at the top of the glass in the middle and the ends need to hang out fairly far - you need to get a good grip on either one - perhaps wrapping it around your hand. H. Lube up the windshield flange metal with some dish soap and water or Hyper Dressing. i. Two people - set the windshield - with the gasket snug all around - into the flange. Cord ends should be inside the car. Make sure it's centered all around. ii. One person is going to pull the cords inside to pull the rubber gasket into the interior of the car, sealing it to the interior side of the flange. At the top and on the pillars it'll be set over the vinyl. The other person is going to be on the outside holding the glass in place while the cord is being pulled. That person will use both hands as often as possible, palms down, fingers splayed on the glass. Their job is two-fold: 1. As the cord is pulled, the glass will want to move opposite of the pull (starts at the top, it'll want to move down, when the pull is on a side, it'll want to push to the other side. Exterior person needs to keep the edges of the glass/gasket from moving out of the hole the windshield sits in. 2. When the cord is pulled the glass needs to sink into the frame when the rubber is pulled into the interior. So, a certain amount of exterior pressure can be needed to keep the glass settling inward as the cord pull progresses. J. With the person with hands on the glass externally, the person inside starts to pull the cord. The cord hanging on the right side will be pulled to the left, and vice versa. Pull one cord only. Pull it at a 90 degree angle to the glass. Pull carefully and slowly if necessary. Don't pull so fast that the person on the exterior can't manage keeping the glass in place or help you get the glass to sink into the hole. I'll be easy until you get to the top corner(s). Stop at the corner and pull the gasket up on the inside and get it set into the flange as much as possible. The gasket needs to be pulled outward (like lifting it the same direction as the outside edge of the glass) getting it to set firmly in the flange. That helps the glass pull inward as well. At the corner, go very slowly and swing the cord in a circle as you're carefully pulling corner gasket rubber. Sounds stupid, but it works and doesn't cut the gasket. Once past, make sure your helper keeps the glass from moving out of the hole on the opposite side. Before getting to the bottom corner, pull the gasket into the flange - do it as you go and it'll help. Now pull across the bottom - it'll want to make the glass pop out of the side that's not pulled yet. All this time your helper needs to be getting the windshield to push inward as you're pulling cord and setting gasket into flange. If you have two helpers, it makes it very easy. Keep going around the entire windshield and do the second top corner same as the first. Pressure on the outside. Finish up by pressing firmly down on the outside, and pulling the gasket firmly into the flange on the inside. k. if it doesn't set right - have no fear - just remove it and start again. Pull the gasket rubber on the inside down on one corner and push that corner out carefully - continue around the whole windshield, take a deep breath, lube it up, try again. (But... It's a LOT easier if you're patient and get it right the first time...) L. Push the gasket out as far as you can - especially at the top corners. Install the trim corners and gap cover pieces. The stainless steel trim is not just for looks - it helps maintain the gasket in it's proper place and will help stop the gasket from pulling away from the top corners. Don't use it at you own peril... Note: I do not use any adhesive or gasket seal. These gaskets were designed to seal around the glass and flange without it. Now, I'm fully aware that that isn't always true. BUT, Arizona (no rain) and Z owners here wouldn't (don't) drive their Z's in the rain even if there was. Okay, they still wash their cars, but heat and NO humidity dries things FAST here. YOU can decide for yourself if you want to use such a thing - Nissan did - in spots - on the later models. I still don't. And: Patience is the key to Joy... Fortune cookie...
-
Replacement Windshield Options
Agree 100% We have pulled (and re-installed) DOZENS of windshields. They're not glued in. The glass can be removed safely EVEN IF the gasket is hard. (And believe me, in the desert South West the rubber is always baked to a crisp!). One can cut the exterior of the gasket, remove the trim, and cut around the glass without chipping the glass in any way. The glass can be lifted out once the exterior of the gasket is removed from it. Then the rest of the gasket in the flange can be removed. With a new gasket, windshield reinstallation should be easier than getting it out. Hell, with a flexible gasket, we've removed the windshield with the gasket in place - and reinstalled it. Patience is the key to joy. Once we had a Z come in with small crack on the upper left tip (only in the top layer of the glass). No replacement windshield, so we had to pull and reinstall it with the crack. EDIT: I have a Pilkington warehouse nearby and with covid they changed their inventory system. So, when I stopped in they couldn't even find Z glass in their computer system or catalog. I spread that word - but - we have a retired glass guy that has provided us with glass for years before he retired. He just looked up the old part number, called the wholesaler and found that they had 4 in stock. They don't anymore... (but I didn't actually get the part number from him - my bad)
-
Interior roof and pillar trim
When we pull that vinyl the thin foam always stays glued to the metal... I think that's the easier route. I've done a few and I glue the foam to the metal and trim if I need to - then do the vinyl. The vinyl needs to start inside and be stretched out to the flanges. Glue it to the flanges. Inside up top it's held with the clips. Remember that the windshield weatherstrip is going to go over the vinyl and when it does it'll pull it tighter - so don't worry if it seems a bit "puffy" (can't think of a proper way to describe a new vinyl install without the gasket in yet...). And the door weatherstrip will cover and pull the A pillar vinyl smooth and tight on the outboard side. The top of the A pillar can be a bit troublesome - getting the joint with the front to look correct and smooth. Remember also the visors will pull the vinyl a bit too when mounted so they may help smooth things out...
-
Header wrap question
That's too bad, stock clutch fan and shroud is a better way to go. That being said - I've had a few radiators now (stock, stock 280, champion aluminum x 2) and the absolute best is my current Koyo Radiator. Awesome design, uses two lower radiator hoses (trim one to fit the upper) cools phenomenally. Mine: Early 260Z (so 240Z style radiator core support), L28ET, intercooler, stock clutch fan, no shroud (should try to make one someday...), Factory A/C converted to 134a, Phoenix Arizona, Phoenix Arizona, Phoenix Arizona, daily driver (I have to take it to the shop...). Doesn't overheat in the 110+ degree temps of rush hour freeway or stop-and-go on surface streets with the A/C screaming (Kia blower, Hayhurst Ultra Heaven center duct). And, yes I wrapped my header and down pipe back to the CAT. Not so much to lower under hood temp but to help cut cabin temp as well. I don't quite understand the Water and Rust worry as even if it got wet the exhaust temps would melt that away in a heartbeat and how's it gonna get wet again? But then, we don't have that particular problem here...
-
240z floors in a 280z
The 280Z floor has a recess for the fuel and brake hard lines that the 240Z floor lacks.
-
Showtime
Yup, Island Park, Mack's Inn, and on up to West Yellowstone. When I was a kid there was a A&W Root Beer Stand in every small town along the way - Salem, Rexburg, St. Anthony... My sister just went to Old Faithful and sent some pics of bears - glad they returned to the Park. They were a huge part of our Yellowstone experience as kids.
-
Showtime
Ah, Layton... I've driven past it hundreds of times... Grew up in Idaho Falls, Mom was from SLC.
-
Fuel and Temperature Readings
What Steve said, and - In both cases the connectors at the sensors are very often the problem. Neither are weather tight and although you don't drive in the rain - and Arizona - oxidation does happen. Sometimes wiggling the two connectors on the fuel level sender helps, sometimes they need to be taken off and cleaned. The posts on the fuel level sender too. You can never be absolutely sure but the connectors under the dash are far better protected than at the sensors so I always start there (sensors) and work toward the gauges checking the wiring. Since your trouble is intermittent, I'd suspect the sensor connectors and/or associated wiring. It's more unlikely but certainly possible: Frayed insulator on wire, to-dash-harness connector, gauge connector, or inside the gauge itself.
-
Fuel and Temperature Readings
The electrical schematic shows that they share a common ground, but I'd expect that to affect your oil pressure gauge too. No step down regulator on a Z car for gauges. There is a fuse in the circuit but there too it would affect the oil pressure gauge and it looks like your hazard switch as well. Check the body harness & engine bay harness-to-dash harness connectors under the glove box. You could test continuity of each of the sensor wires (Y fuel, Y/W coolant). Otherwise you're in the dash to figure that out...
-
Taillight Gasket Exhaust Leak?
Please NO! For the sake of the next guy that has to remove them! (ask me how I know...) I would also advise AGAINST 3M double stick as well. Instead get just some slim weatherstrip foam from Home Depot or Lowes (closed cell if they have it) and run it around the perimeter or just where you have leaks. It'll squish down to nothing where it needs to and fill the gap where it needs to. And it'll be easy to remove if necessary.
-
Gas gauge not accurate/unresponsive to fuel level change
You're not going to like the actual fix: There are adjusters on the back of the gauge for both low and high ends of the needle. Ya, back of the gauge - so getting your fuel gauge to actually represent something close to the amount of fuel in the tank would require removal of the gauge. Then you need to empty the tank and set the "E". Then you have to fill the tank and set the "F". Then you have to reinstall the gauge. In 10-20 years you'll have to do it again because the resistance of your wire and connectors will have changed... And that's why my fuel gauge shows 7/8 full when absolutely brimming with fuel and WAY to the left of "E" when my fuel pump starts sucking air.
-
Impossible Oil Leak?
TPU is a type of 3D Printer filament. It's flexible. I looked at his photo enlarged and you can see the part has been printed. Lucas, our local mechanical engineer, has a pretty decent 3D printer setup and tried to reproduce the boots for the fuel tank hoses under the hatch in his late 280Z using TPU. Stiffer than rubber. They turned out okay but I wouldn't call them ideal. Might work for the oil cap seal but it doesn't print very smoothly...
-
Impossible Oil Leak?
So, none of you people live in Arizona?? Our oil cap seals were dried up, hard as a rock, and leaking 30 years ago. I still haven't found a replacement seal that I really like - most work but are a bit too soft. There's always 400 grit and a hard block...
-
What type of electrical connector does the OEM oil pressure sender have on a 260z
We've seen a couple of those on L engines that have come through the shop. None of them new but they were being used so I assume they worked.
-
What type of electrical connector does the OEM oil pressure sender have on a 260z
FSM says bullet connector and that's what I use on mine.
-
Help with terminal ID on Dash harness
Red/Blue (RL) under the dash is generally for lighting (power to bulbs). Hard to tell from that picture but the location is near the center. My 260Z has a RL/B set in that area for the Map Light... However, the 240Z schematic shows a singular RL to the Map Light (must ground - sorry Earth - to the dash frame?). But, it's probably a light for something... It's too short for a center console indicator and the harness ties up tight to the top of the dash frame so stands to reason it's something near the 3 small gauges maybe.
-
Tachometer Function Question
Kk, corrected my post above.