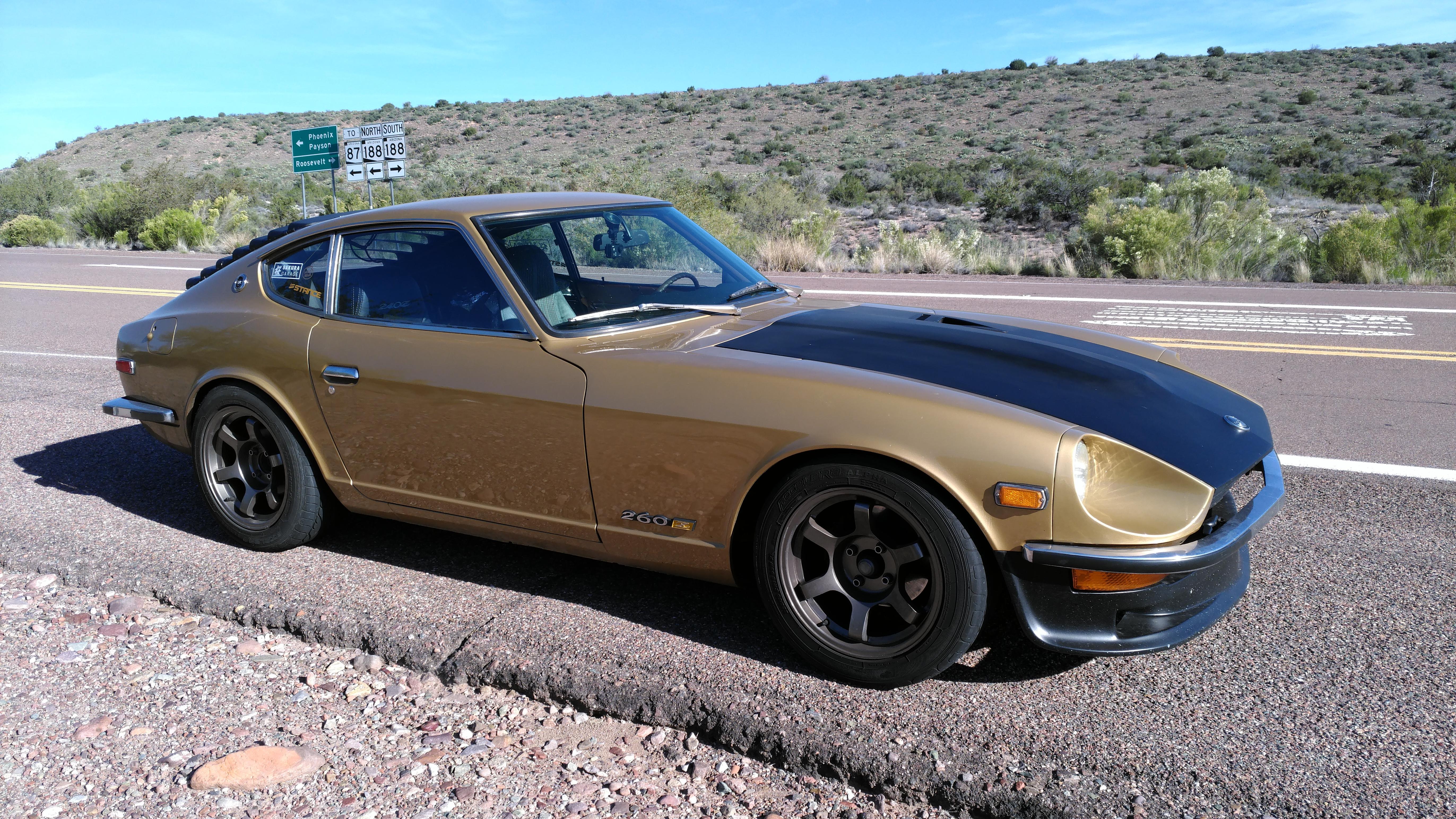
Everything posted by cgsheen1
-
Silvermine dual rear caliper Wilwood upgrade
I heard a lot of "stock brakes are just fine - even if you autocross!" when I first got my 260Z on the road (2008). Then I signed up for a NASA weekend at Firebird Raceway here in Phoenix. My stock brakes were done before the first day ended. (ya, ya, I did need to learn better brake management...) . That prompted my first front brake upgrade: Stock rotors with Toyota 4-piston calipers. Hardly noticed the difference. Small improvement. Disappointed, I then went to the vented front rotor / Toyota wide 4-piston caliper. BIG improvement. Then I installed better friction, more $$ than ceramic, but LARGE improvement with Porterfield pads and shoes. The Porterfields (like many sport or race frictions) were better than stock "cold" (around town) and got really grippy once you got some heat in them. Loved that setup cuz: A. I daily drive. In Phoenix. Not quite as bad as SoCal, but close. 2. Not many people realize how much mountain driving you can do in Arizona - and I do as much as I can. My 260Z Turbo is an uphill beast - the torque of this engine is awesome. But what goes up must come down. My first curvy hilly trip, I came back into Tortilla Flat with a huge smile because my brakes were better at the bottom of the hill than at the top and believe me I used them both ways. My fronts just met end-of-life and I had to replace the pads and rotors after 10 years of driving on them. But, ya, still using my Brembo drums in the rear.
-
Loss of acceleration when hitting gas hard
Remember that the FPR should maintain a 36.3 PSI difference (balance) between the fuel pressure and manifold pressure. Your manifold pressure (vacuum) is lower at idle and under low load so fuel pressure is that much lower than 36.3 PSI. (at 10 PSI of vacuum the FPR should be maintaining about 26.3 PSI on the fuel) At heavy load the manifold pressure decreases, so to balance, the fuel pressure increases. (so, at 1 or 2 PSI vacuum, the FPR should be keeping fuel pressure at 35.3 or 34.3 ish respectively) Once you go to a positive manifold pressure (boost) the FPR should add that positive value to the fuel pressure. Ask me how I know. 🤠This may not apply but it's always something to consider. A long time ago as an apprentice plumber I learned about fluid pressure and rate of flow. Two pipes: 1/8" and 1/2" - they can have the same fluid pressure applied, but the 1/2" pipe will always be able to deliver a higher volume of fluid. This may apply IF there is an unseen obstruction inside the fuel pipe or tubing. Pressure may read at an appropriate value but the system may not be able to deliver the volume needed at certain times. The pressure will only show a decrease when the demand outstrips the ability to supply. (this happened to me as my fuel supply hardline was over 1/2 plugged with corrosion inside at a point near the firewall - difficult to diagnose and pinpoint)
-
Anyone seen these seat covers?
Leather? Stich - the auto upholstery guy a few doors down from our shop in Tempe could have reproduced those but I think he's retired to Bisbee...
-
Condenser failure
IF you powered the coil direct from the battery THEN you literally removed both the ignition switch and the tachometer from the circuit (thus from the equation). (to be clear: removed the B/W wire from the "+" side of the coil, replaced that with a wire direct to battery positive for a short period WHILE TESTING only) The problem is then isolated between the "+" pole of the coil -> to the distributor (and it's connection to the block which is where it gets it's ground connection).
-
Where To Make Cuts
Exactly. I'm not quite 1925 old. That was my Dad. I was raised in the 1950's and 60's... 2 cents is what we got for each pop bottle we found on the roadside and turned in at the store. A little collecting and you got a pretty good stash of penny candy - or even a candy bar for a nickel...
-
Where To Make Cuts
I'm old. When I was a kid we could get 4 hamburgers for a dollar. Ever heard of "penny candy"? We used to buy it... Between then and now my "2 to 45 cents" is probably way wrong...😉
-
Where To Make Cuts
Sorry, not sorry, this doesn't make any sense. Both the roof skin AND quarter skin are very desirable pieces off a donor car. And you don't need to sacrifice one to get the other. "A" pillar, cut anywhere. "C" pillar, or whatever you want to call it, cut at the joint between the roof skin and the quarter skin! It's easiest if you melt the body lead out with a torch. Propane will do - it'll even melt with a heat gun. Then you can see the actual joint. When you have the skins separated it's easy to see how to transplant them to another Z. Unless one is trashed, save both. Just my 45 cents... (inflation)
-
Where To Make Cuts
Every roof skin that I've melted the lead out of has had a weld - not spot weld - under the lead. The roof skin has been bead welded to the quarter skin (and probably whatever else is there also). But, cut it at the weld and it gets re-welded when it's replaced. That's too bad about the rust damage at the windshield. It looks like a nice skin otherwise. Oh, and yes - the body lead is at that junction that shows on the hatch. With a little heat it will become evident. There's also lead on the A pillar in various places.
-
Condenser failure
The coil only gets battery voltage at when the key is turned to the ON position, correct? No voltage otherwise? (The B/W wire(s) on a Datsun should have battery voltage while IGN ON - otherwise zero voltage) This is a fairly simple circuit (considering they looped back the battery voltage feed for the coil from the ballast to the Tach and then to the coil). A couple of things: It's a coil. So when it has battery voltage on the "+" pole, it also has battery voltage on the "-" pole. Which if you connect that (the "-" pole) to one side of the points, it also has battery voltage there. The coil is "fired" by very very very briefly connecting that pole to ground. Check your ground circuit from the distributor to the points, through the points, and through the wire to the coil (removed from the coil for the check). Also check that the points actually break the connection to ground. My final thought is your point gap which at .50mm is at the upper end of the ".40mm - .50mm" spec. - You might try reducing that to mid-range and see if that makes a difference. I vaguely remember back in the mid-70's that I had to buy a dwell meter and learn how to use it for my stinking Ford 351 Windsor engine which I had to tune every three months. Just one reason that once they invented EFI I never went back to a carbed and/or points vehicle... Wait. You get one spark when the ignition is turned to ON? Doesn't that mean the coil "-" is getting a ground right at that moment? Where is it getting the ground? Are the points closed at that time? Perhaps you should check the coil sparking by manually creating the spark condition.
-
Condenser failure
Don't fixate on the condenser. In fact, remove it until you get your spark problem sorted. It's job is to help eliminate radio noise, not make the coil spark... But, you can see from the above schematic that a bad condenser can permanently or randomly GROUND the coil thereby negating the operation of the points. You don't need it (you may want it, but you don't need it...). If you remove it while troubleshooting, it's one less variable. (thanks for the comments and correction - edited the above to make a bit more sense)
-
Where To Make Cuts
We saw quite a few Z's here in Arizona (and coming from California) that previous owners had "sun roofs" installed during that era when they were a thing. After 20 or 30 years the "sun roof" leaked - and no replacement parts. So we did a few roof skin transplants from donor Z's. If you remove the roof with the underneath skeleton intact you can drill the spotwelds on the donor from the bottom (drill the underneath skeleton to separate the skin - thus leaving the donor skin mostly unharmed. Drill the damaged skin (or skin to be replaced) from the top thus leaving the roof skeleton intact on the project car. Cutting at the junction between roof skin and quarter skin is fairly simple once you remove the body lead (melt the body lead out) that covers this junction. And it's a great place for your weld when installing the donor skin since it's going to be covered with fill. With the A pillar, the replacement skin will only require a small weld that's easily ground down and smoothed in - if you remove just the damaged skin (or skin to be replaced) and leave the skeleton and pillars intact on the project car. My advice is to remove the roof so it can be used as a donor in this manner. Plus it leaves the quarter panels intact.
-
New to me, 280Z...
I understand the desire to eliminate the stainless steel trim pieces on the windshield gasket (and hatch) but it does serve a purpose - it's not just "decorative"...
-
Where To Make Cuts
Get a propane torch and go back about 3-5 inches on the rear pillars above the quarter windows. Melt the body lead out and you'll see the welded junction between the roof skin and the quarter skin. Cut through the rear pillars there at the junction. Just go down a bit on the A pillars and cut through there. Turn it over and drill out the MANY spot welds and you can pull the entire roof skin intact off the roof skeleton. OR - give it to someone else that way and leave them to remove the skin from the skeleton... It's safer to handle with the skeleton still attached.
-
Driver's window glass falling off track
The regulators have a different form factor so the door skin might require modification. Since you have both frames, why not just swap the window glass? Use the good glass in the frame that works with your regulator...
-
Lazy Tach with 280ZX Distributor
I also had it in the back of my mind that the stock coil was 1.5 Ohm. I just looked at the FSM: Primary - 1.5 - 1.7 Ohm at 20 degrees C...
-
Lazy Tach with 280ZX Distributor
Pretty much everyone I know here in Phoenix with a carbed 240Z or L-series is now using the 280ZX "matchbox" distributor with their stock tach and no one I know complains about it. There was an individual here famous for his recommendation of that particular swap. I'm NOT a carb guy - gave that up in the '80's - but I been running with these guys for more than 12 years all over the Arizona countryside. I believe I can attest to the fact that the stock 240Z tach will work with a non-point distributor. It'll be interesting to learn why yours will not...
-
Lazy Tach with 280ZX Distributor
Firstly, the fact that it's an L28 or has SU's has no bearing on this distributor swap. None of the Tach rewiring was actually necessary. You really just needed to install the distributor and provide it's wiring. The 240Z Tach is "sensing" the current drawn by the coil. It would make sense to use a stock coil or equivalent. The 280ZX "matchbox" doesn't care about the coil. (It's operation isn't affected by the coil). It also may make sense to leave the stock ignition wiring in place as well - as the Tach thinks it is... Secondly: You can indeed test the ignition wiring. Remove both B/W wires and the G/W wire from each other and the coil. Isolate them. Turn the ignition switch to ON. Test those three wires with a multimeter. ONE of the B/W wires should show BATTERY VOLTAGE. The other two should show ZERO voltage. (Originally the B/W with voltage at IGN ON would be connected to one side of the ballast resistor, the G/W to the other side of the ballast resistor. (which THEN goes through the Tach) The B/W showing no voltage (at the time of test) should connect to the "+" on the coil (this actually comes FROM the Tach). (The "start signal" (+12v) originally would bypass the ballast to deliver un-resisted battery voltage to the coil for starting)) It's your call whether you put the ballast back and wire it up stock OR just connect the B/W that gets power at IGN ON to the G/W wire and put the other B/W on the coil... I prefer making things as simple as possible by NOT introducing EXTRA troubleshooting steps SO I would make things stock and troubleshoot from there.
-
L28 front cover
Yes. Get the engine to true TDC and mark it both pully and distributor. Please don't leave the oil pump attached. You'll have to realign the distributor spindle with the crank gear regardless. This is a lot of work to repair a small leak that's not under pressure so I recommend that you get another head gasket. You'll only use the front bit as a new gasket for the front cover - and discard the rear - so you don't need to go crazy with the type, cost, availability. Remove the front cover and clean all the mating surfaces scrupulously. Cut the head gasket at the block / head junction with a very sharp instrument - careful with the underside of the aluminum head. You want it cut very cleanly & tight against the block. Use that piece as a pattern when cutting the front off the new head gasket but make it just a hair longer on both sides to be sure. And make sure the cut is SQUARE. Clean the face of the block and underside of the head scrupulously. Use Acetone or lacquer thinner on lint free cloth or towel to remove oil and residue on ALL the mating surfaces. Especially underside of head and block where they meet. Check your new mini head gasket for fit and adjust if necessary. Prepare your gaskets (new head mini gasket, right and left front cover gaskets) by THINLY coating them with fuel and oil resistant gasket maker. I recommend the "pinch method" - latex gloves, put a dab of gasket maker on index finger, pinch with thumb and rub a bit, pinch the gasket between your fingers to cover both sides with a thin coating as even as you can get. Then add bit more to that corner between the head and block - make sure the new head gasket seam is sealed when you place your new gasket piece in place. (That's most likely where your current leak is coming from.) The top corners of the cover need your attention. When you put the front cover in place don't tighten all the front bolts first while you're doing it. You want a good seal between the head and front cover and the only clamp is from those two small bolts on top. Snug the front cover in place by alternating pressure on the block face and head underside to pull the cover into that corner made by the block and head. Snug each direction a bit while the cover can still move slightly so you're sure you get a good clamp to the head. Then you can put everything else together. I've noticed that most L engine oil pans have been mis-torqued and the metal is deformed around many or all bolt holes. I pound them back down level with the mating surface and use the same pinch method to apply gasket maker. (Ya, I've tried doing them dry but,,,) (I've done this by trying to leave the head gasket front in place and also have been on the receiving end of someone else leaving the head gasket front in place and trying to re-seal it after pulling the front cover... After all that work, I prefer a method that's more likely to maintain a good seal. That's why I now replace with a clean, dry section of gasket. I use the pinch method for gasket maker on gaskets because I've seen way too much silicone squeezed off gaskets and into places it should never be. Lastly, these engines weren't built for modern oils (synthetics) which don't have the necessary polymers to plug up the minute gaps. So they need all the help they can get...)
-
Installing hatch glass- not working
The hatch glass is a bit tricky because the end opposite of your pull wants to push out of the hole. We've always done it with the hatch mounted and you really need some help keeping the glass from moving too far opposite of the pull. I used to use very thin diameter cord but found it more likely to tear the rubber if you weren't careful and/or well lubed. I switched to soft "clothes line" (cotton or poly) cord and have been doing it that way for years. It's probably 3/16" or 1/4" and I soak it before use. Easy pull and no tearing. We've done more than a dozen this way. I think my son did one solo one time but I never have... Granny is correct on the constant pressure, pulling the inside rubber outward as you go. We pull a bit of cord, press the glass down while pulling the inside rubber outward to help set the glass as we go. The farther along you get the more the glass will be able to settle so the guy on top needs to keep going back with pressure while not allowing the glass to move out of the hole. We normally start on the top but I don't think that really matters. We also don't lay inside - you can reach the string pull from outside and it's then easier for the pull guy to pinch the interior rubber to the outside helping to set the glass and weatherstrip into final position as you go. Keeping the glass down in the hole is paramount. Slow and smooth is fast in setting windshield and hatch glass.
-
MSA Rear Disc - E Brake
This doesn't make sense to me as pull should be fairly equal on each side. The "Y" configuration of the cable should be self-adjusting (a saddle that the cable can slide in). None-the-less sounds like you need a shorter length somewhere to get them engaged fully. The actuating lever on the caliper looks pretty stout. Maybe some pictures?
-
MSA Rear Disc - E Brake
There is adjustment to the parking brake system. You probably won't like where it's at...
-
280zx dizzy, too much timing advance. How to make it not hurt my engine?
Max vacuum will be at deceleration - idle second highest. Under load vacuum will diminish and cruise vacuum will be kinda middle of the MAP range (Manifold Absolute Pressure). Except at Idle, MAP is always changing and LOWERS when you have your foot in it. I think your assumption that advance might hit 55 degrees is likely unfounded. When the mechanical advance is highest, vacuum advance is nominal. When vacuum advance is highest, mechanical advance is non-existent (except on deceleration perhaps where advance is not likely to be a problem). I'm going by what I see on my MAP gauge - correct me if I'm wrong. BTW - my MAP gauge goes BOTH ways... Oh, and I don't think Zed Head wasn't talking about vacuum ports on the balance tube - he was talking about the port on the carb near the throttle body...
-
Setting rear toe
And probably coilovers with camber plates...
-
Engine Compartment Splash Pan
The three that I have are all the early design part (guess that makes sense). Like the pic kats posted - no holes. I don't have the later part to make a comparison with so I can't comment on if the late 260/280 part could be made to fit the earlier Z's. (But since the "splash-board engine" fastens to the lower core support which changed shape starting with the late 260 AND the radiator also changed size and shape, you'd have to assume the "splash-board engine" requiring a different shape as well. Knowing Nissan, I would also assume that most of the mounting points would remain the same on the frame and cross member.)
-
Setting rear toe
My son ('76 280Z (which was factory Gold Metallic BTW)) used those years ago to adjust the rear control arm as much as they would allow. He lowered his 280Z mightily and even at maximum they didn't bring the toe back all the way (especially on the right side which has always been weird to me). Depending on how much of a change you've made, you may not need to worry about the precision. Just saying... (and since he stuck with stock struts, he never got his camber even close...)