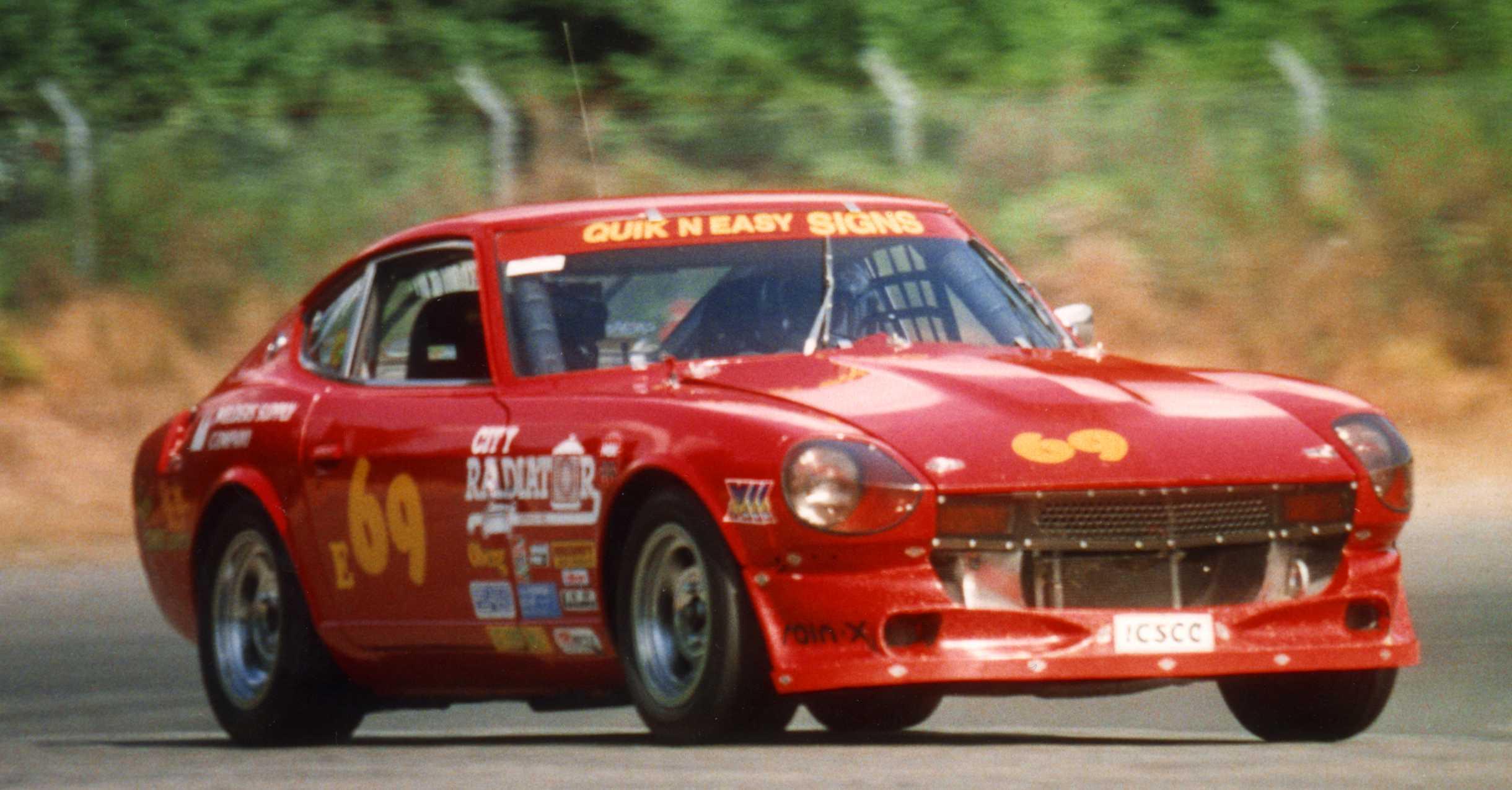
Everything posted by Racer X
-
What is your (most) valuable "made it myself" PART! and most valuable lesson learned about Z-cars!
So. After all that, what was your finishing position?
-
Oversize Pistons
Why not have the machine shop source pistons? They should have the specialized equipment for checking the connecting rods and mounting the pistons.
-
Z's only a mother could love thread
What a bunch of rust buckets. Not much usable structure left on any of them.
-
Z's only a mother could love thread
I’ve seen car alarms back in the day that had a key cylinder on the exterior, but never one creatively placed like the one on this 280Z.
-
Oversize Pistons
Whenever I have had engine block work done, I have given the machine shop the cylinder block, complete rotating assembly (crankshaft, connecting rods, damper pulley, flywheel and clutch cover). The machinist sourced and fitted the pistons. The machinist and I had a clear understanding of what I wanted, including the piston configuration. I was given everything after the work was completed, including rings and bearings, and prior to assembly I checked bearing clearances and ring end gaps.
-
1978 280z brake proportion valve seals
In any hydraulic system the cup side of a seal faces the pressure of the system. That way the pressure forces the seal against the bore and rod.
-
Z's on BAT and other places collection
Wonder why he is selling the engine, bumpers, and the aftermarket carbon fiber bumper?
-
What is the best dashboard treatment ?
Looks like a nice instrument panel. No cracks and unmolested. I would simply clean it with mild detergent, then dress it with a plastic dressing.
-
Let's show vintage racing pictures. I'll start.
Looks like he gained some weight.
-
Let's show vintage racing pictures. I'll start.
Odd. That doesn't look like Paul Loquesto Newman.
-
280Z Steering Wheel
After all that work I’d carve out an adapter to mount the original stuff. Or make something all your own.
-
280Z tachometer problems with a ZX (E12-80) ignition module
Have you looked into one of these? https://www.technoversions.com/TachMatch.html
-
New Member,New to Z's
Vitamin B12.
-
Z's on BAT and other places collection
I’m in the country, on 6 acres, and a private road, so no worries from Citiots.
-
Z's on BAT and other places collection
Looks like the V8 might have been a little bit much for that one.
-
Z's on BAT and other places collection
And a 2+2 in Snohomish for $2,800. Extra intake manifolds. Lots of cancer pics. https://seattle.craigslist.org/sno/cto/d/snohomish-78-datsun-280z/7475720654.html
-
Z's on BAT and other places collection
A V8 Z in North Bend. $28,000 https://seattle.craigslist.org/see/cto/d/north-bend-240/7482946215.html
-
Z's on BAT and other places collection
Oh, you like the digitalis?
-
Z's on BAT and other places collection
-
New project
Since we all seem to be traveling down motorcycle memory lane, here is one of mine. A 1977 Honda Hawk, bought brand new shortly after college. Still have it but haven’t ridden it in a very long time.
-
280Z Steering Wheel
There is a guy on Ratsun, who lives in Texas, that has made a few wood rims for steering wheels. It is a fairly straightforward process. Make a circular jig for a router, select a nice cut of wood, rout the two halves, glue them onto the rim, and finish the wood. One he laminated several different types of wood stained different colors. It looks awesome. He even made a matching shift knob. Check it out here: https://ratsun.net/topic/78921-diy-steering-wheels/#comment-1700673
-
[2022] What Did You Do To/with Your Z Today?
Thanks Cliff. So this site lists, but doesn’t really describe the differences in the green and blue dyed 100 octane avgas. I did find a Shell avgas site that does. So the green dyed avgas is an older formulation that has tetra ethyl lead in it, and the blue dyed avgas has a lower amount of lead in it than the green dyed fuel, hence, the “LL” designation. Sheesh, I learn something new everyday.
-
[2022] What Did You Do To/with Your Z Today?
What is the web page this is from Cliff?
-
[2022] What Did You Do To/with Your Z Today?
Looks like the green must be unleaded. I always go for the highest grade at the pump when I go to the airport to buy fuel, and 100LL (100 octane low lead) is usually the highest grade. I’ll need to have a look when I go next time, and see if they have the unleaded.
-
[2022] What Did You Do To/with Your Z Today?
Blue. It is dyed so it can readily identified by the tax cops looking for people who are trying to avoid road taxes. The racing gasoline I used to buy is dyed purple. Off road diesel (for tractors and heavy machinery) is dyed red for the same reason.