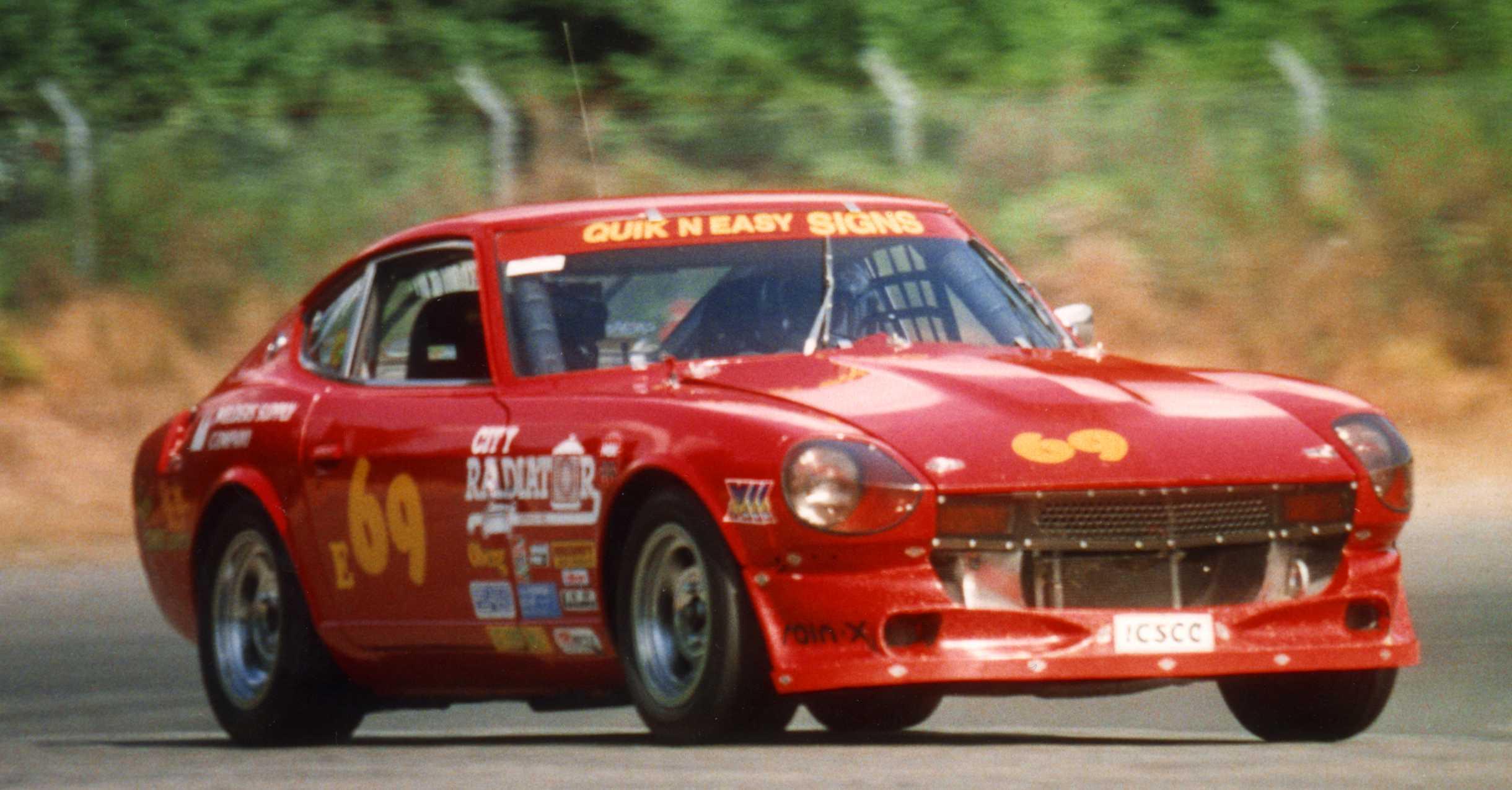
Everything posted by Racer X
-
Best Head
Oh yeah. Isn't that head made from unobtanium? I can only dream of ever having something as awesome as a setup like that. There is that guy who made his own twin cam head for L series engines, 3D cad design, custom casting, CNC milled. I think that setup is even more money. Of course you can spend plenty of money on an E31, P90, N47 . . . . . . . I think I'm into the E31 I have at least two grand when I built my first race engine. Other than new valves (missed a shift coming onto the front stretch at Seattle, on a new bottom end, kissed the valves - now I have a rev limiter) and guide seals, and later a different cam, I haven't spent any thing on it. It has been sitting since the last bottom end had a crank break between the last main and number 6 rod (the second in about 20 years of racing my Z on the West coast) at Thunderhill about 12 years ago. I am thinking of using it, and the race induction setup paired with a header and a bottom end I built for the brown car when I was married to Mrs, Racer 1.0. That engine was going to get a small chamber E88 head I have, but haven't finished yet. It is ironic that when I had the first crankshaft break, it was when I was building that other engine, and was pursuing a championship. So instead of finishing the E88 head, I put my E31 race head and intake/exhaust on it, and raced one meet with it. We had a long enough break before the next race that I was able to build another engine, and swap everything back. In my zeal to win the championship the engine got sidelined. Then I divorced Mrs. Racer 1.0, bought some property, stayed focused on racing and the brown Z and the engine got parked. That was about 26 years ago, more or less. I met Mrs. Racer 2.0 about 23 years ago, and we wound up selling my place, and buying the place we have now, built a house, and the car(s) have been patiently waiting.
-
Best Head
Seventeen thousand bucks for what head?
-
Best Head
When I get some time I’ll try to snag a shot or two. The head has been sitting on the workbench for a few years, waiting for another bottom end to sit on top of.
-
Best Head
Dave Endrigo, Poulsbo, WA. The Flow Technics business has evolved, first to Flo Cat, then to EPD Corp. It looks like he is involved in engine development, but I haven’t talked with him in over 20 years. He has a Facebook profile, but I’m not on Facebook, so can’t contact him. I do need to reconnect with him, as I read recently that his younger brother, whom I went to high school with, has passed away.
-
Best Head
Well, looks like @Wally wins thread of the day, eh? Remember, never ask a wood nymph for a little head. Anyway. Like Cliff says, check out the P79, it has potential. But an E31 . . . . . . . . . . . . . the E31 that has been on 3 engines I built for my race car from 1989 to now. It breathes very well. Dave at FloTechnics ported it for me, larger valves, cc'd the chambers, and had the head, intake and exhaust on his flowbench.
-
California 1978 Datsun 280z Restomod
I see, wasn’t aware that the JDM cars came that way.
-
California 1978 Datsun 280z Restomod
I would get the connectors and wire terminals from that company that has the correct OEM parts, and make up a jumper pigtail for each side.
-
California 1978 Datsun 280z Restomod
Looks very nice Kevin. I gotta ask. You filled in the rear side maker light openings, but left the front ones open. How come?
-
240ZBUILTBYME 1971 240z HS-001063 Project Georgia
You can call me Racer. Aw, shucks, yer makin' me blush. The variance comes from production tolerances, or the difference in size from one part to the next, for each of the thousands of parts that make the whole airplane. Production is carried out inside of buildings sheltered from weather. Although not all buildings are insulated with climate control, the heat generated from the manufacturing activities keeps them at a reasonably consistent temperature day by day. Also, some manufacturing environments are carried out in smaller, insulated and climate controlled buildings to prevent expansion or contraction of parts, such as wing spars, which are over 100 feet long, and could change in length a great deal even under only a small change in temperature. So a 747-800 (the current model) is about 250 feet long. The fuselage is assembled from a few dozen exterior panel assemblies each made from a few hundred components (skin panels, frames, stringers), hundreds of floor beams and longitudinal beams, the longest being around 25 feet long. Also. when the bolts and rivets are installed, the metal around the holes is displaced, causing some deformation, and elongation, of the parts (this is accounted for in the engineering design). Although the size of the holes are always the same, there are still tolerances, and no two holes are exactly the same size. Additionally, the fasteners vary a bit in size. And when a rivet is driven, or a bolt tightened, again, no two are exactly the same. So add up a few thousandths of an inch over 250 feet and all the many parts, and 18" isn't much. ~~~~~~~~~~~~~~~~~~~~~~~~~~~~~~~~~~~~~~~~~~~~~~~~~~~~~~~~ By the way, if you ever find yourself riding in a 747, go to the very last seat at the back, on an aisle. While the plane is taxiing, lean out and look towards the front of it. And during takeoff and flight, do it again. Observe the floor. It will twist, ripple, undulate, and curve up and down, so much so one might wonder how it can move this much and not break. A similar thing can be observed while sitting at a window near the main wings, watching the tips rise and fall, and if one looks closely enough they can be seen to flutter or twist. Relax, they are suppose to be flexible.
-
Hatch Emblems
Awesome idea! Maybe @CanTechZ could mail you a copy of his template.
-
Z's on BAT and other places collection
That's what I was thinking. Or that the quarter panels were replaced. It is in Illinois . . . . . . Interesting they show the engine number on the original invoice , the plate in the strut tower, but not the pad on the engine block with the engine number.
-
Let's show vintage racing pictures. I'll start.
The man that wrote the book! Awesome.
-
240ZBUILTBYME 1971 240z HS-001063 Project Georgia
I am a structures mechanic. Anything that is part of the airframe is what I (we) work on. As aerospace machinists our job is to fit and assemble commercial jet airliners, freighters and tankers (for the military). So far I have been part of the manufacture of the Boeing 777 (wings and fuselage), 777X (fuselage), and the 767 freighter and its derivative the KC-46 tanker (fuselage). The airplanes are assembled in huge jigs, we call them “the tool”. The 777 wing assembly jig is huge, 4 stories tall, with a footprint larger than an American football field. 4 pairs of wings are assembled simultaneously. So the machinists are working “in the tool”. The wing spars are also assembled in a tool, about 60 feet wide and 120 feet long. The 767, 747 body sections are assembled into larger sub assemblies in large 4 story high tools, similar to the wing assembly tools. The legacy 777 (metal wings) was assembled in a similar tool, which was removed and replaced by crawlers for a “moving” assembly line to also build the 777X. After the wings and fuselage sections are complete they get joined at wing/body join, then final body join. At each step the various pieces are loaded into the tooling, positioned using indexes and checked with lasers to the nearest 0.001”. Still, when an airplane is complete, due to manufacturing tolerances, each one is different in length. I’ve read that a 747 can vary in length by as much as 18”. So I suppose that none of them are perfectly straight, but all modern airplanes have provisions to trim, or adjust the airplane for straight and level flight. The engines are manufactured elsewhere, and installed on the airplane by engine technicians who specialize in the hookup and installation of the engines.
- 240ZBUILTBYME 1971 240z HS-001063 Project Georgia
- 240ZBUILTBYME 1971 240z HS-001063 Project Georgia
-
differences between 240 and 280 steering racks
Ratios and proportions were always difficult math for me. I really struggle(d) with math, and yet I pursued a career in engineering (shortly) and then became a mechanic/machinist. Go figure. Anyway, as I understand it, the ratio for something (as in gearsets and pulleys and other mechanical things) is the difference between the movement of one part compared to the other. Or, In mathematics, a ratio indicates how many times one number contains another." As the good Captain points out, Moog defines the ratio in terms of degrees. 360 degrees divided by the 20 degrees the wheels turn equals 18, so the ratio is 18:1. So if the rack moves the wheels 24 degrees for one turn of the steering wheel the ratio would be 14:1. I think I got that correct. A bit easier than calculus, trigonometry or descriptive geometry (the math behind geometry).
-
saturday night music thread
I saw Golden Earring at the Paramount in Seattle way back, late 1970's, early 1980's, something like that. They had two of everything. Drummers, horn section, bass, rhythm and lead guitars, keyboards. It was a wall of sound, and pretty trippy. Of course mind altering substances might have been in play too, but the double we were seeing was real, not blurred. Awesome performance. At a great venue. Live music is best.
-
Suspension Cleanup and Refurb
PBA strikes again.
-
saturday night music thread
I'm feeling socially distorted today.
-
saturday night music thread
This be me on an occasional Saturday.
-
Suspension Cleanup and Refurb
A bit late to the party . . . . . For what its worth, I use a press if available to push the wheel studs out. Less risk of damage and the studs can usually be reused if otherwise in good condition. Use the press to reassemble. If a press isn't available, you can use a square of 3/4" plywood on the shop floor, set the hub on it with an mag wheel old lug nut on the stud a 1/4" or so, and beat the stud out with a brass hammer. Use the hammer and a drift to reassemble, and the old lug nut and a few flat washers to pull them all the way in (smear a dab of grease between the washers to reduce galling).
-
Failed CO emissions - all controls removed - where to start?
Did you check the coolant temperature with something besides the gauge? If you don’t have a non contact pyrometer, you could try your hand, but isn’t as precise as a pyrometer. It could be the thermostat is stuck open. That would also cause the engine to run too rich, as the ECM would think the engine is cold and enrich the fuel mixture.
-
Failed CO emissions - all controls removed - where to start?
The hydrocarbons are extremely high, even for an older engine. Hydrocarbons are unburned fuel, so you need to work out if the injectors are simply delivering too much fuel, or if there is a reason why the mixture isn’t getting burned more completely.
-
Looking for opinions of this set up
Looks interesting, but I don’t see how it will make any difference with regard to the bottoming out of the struts. And, it looks like it will actually raise the ride height an inch or to.
-
saturday night music thread
Say goodnight Gracie.