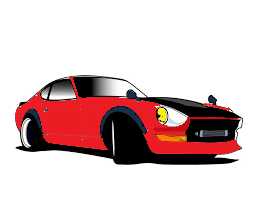
Everything posted by Jeff Berk
-
R180 Differential drain/fill thread size
Does anyone know the threading size for the differential drain and fill plugs. I tried to measure them and came up with 27x2.0 but apparently this was incorrect. My "Thread Detective" doesn't go this high.
- Driveshaft noise
-
Does an LSD need better cooling?
Great mod! Any chance you still have that CAD file? Its a shame to cut up the cross member just to get the two saddles. Great paint job! I've been tempted to get one of the inflatable paint booths for the back yard or create a booth in the garage like you did. For now, I'll stick with vinyl wrap.
-
Does an LSD need better cooling?
Patcon, I've been going through the pages of the Lily build and have not spotted that part yet. Can you give me some direction on where that section of the build thread is? Jeff
-
Does an LSD need better cooling?
That cross member supports the transverse links which gives me pause. It might be possible to create a standoff to shift the cross member 2-3 inches to the rear. The question is: Does the improvement in heat dissipation from the LSD worth the change in design of the vehicle's suspension supports? It looks like this R200 finned cover had the same issue and required modification as well: https://protunerz.com/products/protunerz-billet-r200-finned-differential-cover My son's partially dissembled Lotus is back under the Z again making this more difficult.
-
Does an LSD need better cooling?
Back to the drawing board. I got my son to push his '05 Lotus out from under my Z which is up on a lift so I could check for fitment. When I tried to fit a prototype onto the mounting points I realized that there is a cross member below it that is in the way. I'm not sure what I can do other than greatly reduce the reservoir volume and size of the heat exchange fins.
-
Does an LSD need better cooling?
I saw that video and I included mounting points on the fins to attach a removable 1/8-inch thick scoop. I drilled out the fill plug and treaded it for a temperature sensor so that I could experiment with it during autocross to evaluate the effect. Anyone know the threading on the fill and drain plugs? I'm going to need to order a tap. I also need to locate the fill plug I tapped and promptly misplaced. My shop is a tiny corner of my garage and I still manage to misplace things.
-
Does an LSD need better cooling?
Right now it's looking at about eight pounds. I'm using the software to apply fillets where I can and I'll round the remaining edges post printing. The attached obj file is a viewable 3D file. It can be viewed using Paint 3D although it takes a couple of minutes to load. The stl file might work better depending on your software. differential with draft Rev 3 v5.obj differential with draft Rev 3 v5.stl
-
Does an LSD need better cooling?
CO, Emmanuel didn't seem too concerned about the areas you marked so I'm assuming draft is not too important if the depth of that portion of the mold is not too great. I'm also not too competent in using Fusion 360 so adding draft in some areas could take me hours, if not days to figure out. In some cases, I've had to scrap the model and start from scratch. I'm currently struggling with modeling a channel to promote fluid circulation from the spinning ring gear. What is shown in this version is actually a model of the cavity. The solid portion of the channel will be covering it and then I'll change the channel part to a "cut". I'm sure the shell command would work better but I'm not too proficient in its application. Time is running out because Emmanuel only does aluminum castings every 3 to 4 months. If anyone has a suggestion, please speak up. Jeff
-
Does an LSD need better cooling?
CO, Thanks for showing that. I think I have it fixed now. I used the drift feature in 360 Fusion to the angles until they changed from red. I'm considering adding a channel to aid in the flow of fluid that's splashed up by the ring gear. Grannyknot, You mean a group buy so we can get this part even cheaper? Lets wait until at least we see if this part works. Also, keep in mind that (1) a lot of post-cast work is necessary, and (2) I don't know what I'm doing. Jeff
-
Does an LSD need better cooling?
I just got a call from Emmanuel at Cattail Forge and his only suggestions based on the 3D print I sent him were to add draft to the cooling fins along the bottom and to create the holes for the mounting studs using a template post casting. He also said that I should assume 1.3% shrinkage (there's that image again). I confirmed with him that labor would be about $35 and the aluminum was $3 per pound. His next aluminum forging will be in about 4 weeks.
-
Does an LSD need better cooling?
I originally tried to use a 3D scan but that got to difficult using the available software so I started from scratch. This is likely my 3rd iteration of the part. The problem with the version in Post #16 was the expanded reservoir did not have enough draft and the only way to add it was to redo much of the reservoir. The internal bracing was mostly eliminated because I felt the one I was modeling seemed to be thick enough. The internal fins were intended to provide better heat transfer and also some internal support. I was considering adding some internal channeling in the next iteration along with suggestions offered by the forger.
-
Does an LSD need better cooling?
CO, Thanks for the review. I agree about the mustache mounting holes. The fill hole is offset from the internal fin. The Inspect>Section Analysis feature in Fusion 360 was handy for positioning these features. Unfortunately, I didn't spot the Inspect>Draft Analysis option in Fusion until after I printed the part. I noted a few faces that looked troubling in the analysis in my letter that accompanied the part to the forger. There's a steep learning curve with Fusion especially if you are not a CAD person. Unfortunately, it looks like you and the forge are about 6 1/2 hours away. Jeff
-
Does an LSD need better cooling?
I just got the prototype printed. It took ~45 hours and 450 grams of PLA plastic. I test fitted the cover on my diff and there was a clearance issue that I'll need to address in the next iteration. I'm sending it off today to the guy in PA with a forge for him to offer suggestions. That brings up the question, is an operator of a forge called a forger?
-
Does an LSD need better cooling?
I don't fully understand the process but I'm sending the caster a 3D printed part for them to create the mold. Its tempting to visit the caster's forge but its a 5-hour drive.
-
Does an LSD need better cooling?
That adhesive is about $100. I actually have some conductive adhesive for attaching aluminum heat sinks to electronic components. I might give that a try and see if it helps during an Auto-X (and see if they stay attached).
-
Does an LSD need better cooling?
I did look at the Banks video and borrowed some ideas from it like adding an under differential air deflector. His temperature studies also was the reason why I added a temperature sensor to the fill plug. I'm planning on using the original diff cover and observe the temperature during one or two Auto-X events. After that I need to change the oil and I was then going to try the new cover and see how it impacted the temperature measurements.
-
Does an LSD need better cooling?
Thank you for all the input. My knowledge base for casting is at the low end as I’ve never had casting done for anything, but this is a chance for a new adventure of sorts. I’ve modified the design based on comments, and I was planning on printing a 3D test piece to send to the caster to review. I recall that he said to keep parts to ¼ inch or thicker and to have a draft as CO called it to make it easier to separate parts from the mold. I think that the concern might be that the separation of the 3D printed part from the sand to form the mold and not the separation of the cast part from the sand, but what do I know? Besides external fins, I’ve also added fins to the interior to promote heat transfer between the fluid and the aluminum although aluminum to air is likely the more important thermal transfer concern. The interior fins should also add strength to the bulbous oil reservoir. I was planning on doing all the drilling of the holes post casting. With all the points CO brought up, I think this part is not going to happen for a few months while I research the process a bit more and communicate with the caster.
-
Does an LSD need better cooling?
When I called in December they said they will be doing aluminum in 3-4 months so they are likely a very small, busy operation. I'm going to enlarge the entire structure using a percentage of around 6.5% to allow for shrinkage*. I guess if dimensions are critical, you don't use cast aluminum which is likely why you need shims when assembling a cast aluminum differential. *Every time I see the word shrinkage I think of that Seinfeld episode.
-
Does an LSD need better cooling?
My worries about the fins was that I don't know how thin I can make them. They are 4mm across the top. I was warned that they need to be tapered to allow them to release from the mold. I have a spot on two of the fins where I can attach screws to mount an air deflector to direct air flow from below the differential across the back. I don't know much about casting but my understanding is that the Cattail Foundary uses sand casting. They only do aluminum every few months so it might be a while for them to get to doing it. All they need is a 3d print that is scaled to account for shrinkage. https://www.lancasterfarming.com/country-life/antiques-and-history/cattail-s-customers-come-from-near-and-far/article_bfdbf807-69b1-5194-9fee-762e003d46dc.html Back to my original question, does the presence of an LSD heat up the differential more than an open differential? Should I increase gear lash slightly to account for the increase in temperature? I notice that my gear lash (pinion to ring gear) decreased when I installed the LSD so I had to do some shim adjustment.
-
Does an LSD need better cooling?
I'm getting back to installing an LSD in my R180 but I was concerned about the LSD heating up the differential during Auto-X. I drilled/tapped a hole in the fill plug for a temperature sensor but I also was looking into an alternate differential cover with extra volume and cooling fins. I located a family-run foundry operation that will do a one-off aluminum casting for $40 plus $3/pound so I designed one. Anyone want to comment on the design?
-
Quaife LSD Installation in R180 - With Questions About Installation Also
Yellow vs Prussian blue marking compound My local auto parts store only had Prussian blue. I tried it for marking my ring gear but it seemed to be difficult to observe a contact pattern. Would yellow of been a better choice?
-
My Z has a new stablemate
At the time I was too confused to be terrified. I had my seat reclined and I was covered with my winter coat as my son refused to turn up the heat. Then I heard "Dad, Dad... my steering isn't working". Luckily the turnpike was neither curvy or crowded and we still had a couple of degrees in either direction on the steering.
-
My Z has a new stablemate
My son just purchased a 2005 Lotus Elise. It needs some cosmetic work but is mechanically sound. Its currently stored under my 260Z that is waiting on its differential to be installed. We drove to Chicago from Cleveland to pick it up and had an eventful road trip. On the way there, my son's 2019 Veloster Type N's steering wheel locked while driving at 80 mph on the turnpike. He was able to inch the car to the berm, cycle the ignition off and on and that cleared the lock. We just found out this morning that there is a TSB that covers a slew of Hyundai models that addresses this concern so its sitting at the dealer waiting on a part. Please ignore my junk filled garage in the photo.
-
KAAZ R180 LSD fit problem
How many times have we all felt like an idiot when working on our cars? 😀 Did I ever mentioned how when I first purchased my Z I immediately changed the oil but didn't notice that the gasket from the old filter stuck to the engine so I had two gaskets. I drove around the block and wondered why there was a trail of oil leading out of my drive. Luckily a PO had installed an oversize oil pan so there was still some left.