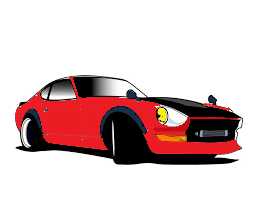
Everything posted by Jeff Berk
-
4-speed: No 1st 2nd gears
Keeping in mind that this is a 4-sp and the attached diagram is a 5-sp, it looks like I have it right although the alignment looks kind of off.
-
4-speed: No 1st 2nd gears
EuroDat: I'm not sure I'm understanding your last paragraph correctly. I've attached 2 photographs of the transmission showing the location of the forks and the striker end of the fork rods. The striker end does not look right but I think I have them in correctly. I'm not sure if I was able to shift the transmission into 1st or 2nd, but the transmission definitely did not seem to click into those positions. I might of been in neutral when I thought I was in 1 and 2 gears. Jeff
-
4-speed: No 1st 2nd gears
I just installed a used 4-speed to replace a 5-speed that is no longer functional (long story). I opened the 4-speed up to replace the input shaft bearing because it had been exposed since the transmission was stored without the front cover and I thought some dirt may of gotten into the bearing. I had to remove the three fork rods to pull the bearing. I noticed that the 3rd 4th rod seemed very tightly stuck into the adapter plate as were the detent balls in the vertical hole between the shafts. I reassembled the transmission and discovered no 1st or 2nd gear. I pull the transmission and checked to see if the roll pins were in place and they were. The 3rd 4th fork rod (middle rod) was still difficult to slide through the adapter plate and the detent balls between the upper and middle rods required a long punch and a lot of force to push them through the this section of the vertical hole. I've ordered an 8mm hone to try and clean up the vertical hole assuming that the detents are not moving out of the way to permit the 1st 2nd fork rod (upper rod) to move. Is there anything else I should check out. This is now transmission #4 so I'd like to make some progress on this one. Between this transmission and my chainsaw, I'm not sure which is more frustrating to get operating. Jeff
-
Headlight covers: details of design
I looked up one of the old threads and saw where someone was planning on manufacturing these and gave up. That's why my plan is not as ambitious. From the photographs, it looks like the cross section is similar to what I have attached and the width is 3/4-inch. I'm assuming one leg is shorter than the other to accommodate a rubber gasket that would hold the cover in place.
-
Headlight covers: details of design
I'm in the middle of some repairs on my 260z and am already looking towards the next challenge. I'm trying to understand how the lens cover frames are constructed or better, how to reproduce them. I'm assuming that they are stamped and then stamped a second time to form the curves and finally chromed. Can someone sketch for me the cross section through the frame or a good photograph of the back side of the frame to show the detail of its shape. I have some ideas on how to reproduce a pair without having to resort to having a mold made and using a stamping press that I'd like to explore. If I can figure this out, I'll publish the methodology but I do not plan on selling these.
-
Oil pan removal question (oil pickup?)
From his documentation, it looks like PO2 took really good care of it. PO3 bought it for his son 😏, enough said. On a side note, my neighbor across the street recently purchased his college-age son a 26-yr old 300Z twin turbo. At least it's an automatic so he can't do too much damage to it.
-
Oil pan removal question (oil pickup?)
Grannyknot, In '86, the second owner installed the pan as part of a spare-no-expense overhaul. Since then, many of the parts were removed due to various reasons. The triple Webers, Recaro seats with 6 point harness, red high-pile carpeting 🙂, racing cam, and now the 5-speed are gone. The PO did invest in a new 280z engine (bored 20 over, new pistons, polished, balanced) and I'm almost positive it is still in there. Most of what was originally done is listed in a dot-matrix printed summary 2 1/2 pages long dated 1987 at 51,000 miles. The third owner hardly drove it and when I got it with 74,000 miles, the Centerforce clutch and flywheel were already shot. I don't know if I can bring it back to its glory days, but I'm going to make an effort at it. Jeff
-
Oil pan removal question (oil pickup?)
I got the oil pan off! The PLA wrench i printed didn't work but it gave me the dimensions I needed to get a couple of steel wrenches made. The oil pan is surprisingly complex with several baffles, screens, and 4 spring-loaded flaps. There was hardly any sludge in the bottom of the pan but the car likely had just 40K miles on it since the installation in the early 80's. I still see no reason for the second oil drain plug on top of the tank. I had to remove the plug to get even my modified wrench with a ground-down socket in there. I will need to cut or grind off some of the brim around the oil pan so that I can get that one troublesome bolt back in.
-
Oil pan removal question (oil pickup?)
I have it up on a lift which makes the effort more tolerable. That extra-wide oil pan is a real PIA. I'm trying to get the maker space near me to make a couple of offsets but with C-19, I have to rely on students to fabricate the part. Their waterjet would cut these out in minutes. I might try a 3D printed wrench but I'm not sure a PLA wrench can hold up.wrench offset.pdf
-
Oil pan removal question (oil pickup?)
I'm at TDC, dip stick is out as are all but one bolt holding the oil pan. Unless someone can come up with an idea, I'm having a tool made because nothing I have or purchased can get to that one last bolt. The oil pan lip blocks access using a box wrench and the oil pan's budge doesn't leave enough room for a socket wrench. A flex head box wrench won't lock on possibly because of the pan lip. The exhaust is welded so I'd likely have to cut it to remove it but I gained an inch or two by unbolting the manifold. I'm trying to get a shop to make a short offset for a 1/4-inch drive wrench. The offset from a crows-foot wrench is too short. If that doesn't work, I'm going to give up and put all the bolts back in and refill it with oil.
-
Zx 5 speed rebuild
Could the slipping out of gear be related to a damaged shifting insert spring? That was a suggestion a mechanic gave me when I was having problems with 5th gear. On a side question... What is a reasonable price for a 5-speed that is sold as is with minimal opportunity to inspect it? I have someone who is considering buying a junked car and offering me the transmission if I throw in some money for the car. I'm not sure if there is an opportunity to pull the transmission first.
-
Coolant and other leaks....
You might try water-soluble UV dye. I've used similar dyes in oils and AC leak tracing. https://www.autozone.com/test-scan-and-specialty-tools/uv-light-and-accessories/autopro-antifreeze-coolant-leak-detector-uv-dye-8-oz/835773_0_0
-
Zx 5 speed rebuild
I purchased a 1 1/2 inch crowsfoot wrench and attached it to my 1/2-inch torque wrench so that it was at right angles. This did not change the length of the torque wrench appreciably so the torque value I dialed in should be somewhat accurate. Maybe a little underestimating the torque if you consider the length from the center of the nut to the handle is slightly longer than the center of the wrench head to the handle. Lets see Pythagorean Theorem, a2+b2=c2, a 2 + b 2 = c 2 , can be used to find the length of any side of a right triangle.
-
Oil pan removal question (oil pickup?)
I don't have an engine hoist so this could be interesting. I can picture myself getting one nut on and dropping the second one several times. I'm going to be switching out my transmission as well so I hope that getting that out of the way will give me more room to slide it back.
-
Oil pan removal question (oil pickup?)
I'm going to be replacing my oil pan gasket and in reading up on it, I found a set of instructions that said: Knock pan loose with rubber mallet. Then loosen the two 12mm bolts on the oil pickup. So, do I drop the oil pan a few mm's and reach in with a 12mm wrench and loosen two bolts? Is that so I have some wiggle room to get the pan off?
-
260z rebuilt rack & pinion service suggestion
Thanks, that's a good start.
-
260z rebuilt rack & pinion service suggestion
I'm looking for a R&P rebuilding or exchange service. I'm burned out from my transmission rebuild to do it myself. Can anyone offer a suggestion?
-
wide ratio FS5W71B slipping out of 3rd & 4th
PXL_20210426_183301294.mp3I took it out for a slightly longer drive and recorded the sound in 2nd gear with acceleration and then deceleration. I've attached the audio file. I also noticed that it is slipping out of 5th when I let up on the gas so I'm assuming that means it's not being pushed fully into 5th gear. If all else fails, I have a 4-speed of unknown condition I could try. PXL_20210426_183301294.mp3
-
wide ratio FS5W71B slipping out of 3rd & 4th
I only drove it a few minutes due to concern about the whine. I'm think that by dropping the transmission, if it landed on a countershaft end, damage the center countershaft bearing is reasonable. Next time I'll have my son tighten the vice while I'm holding the transmission while holding the aluminum vice jaws. I just ordered a replacement center bearing. I'll attempt to replace it without disturbing the main shaft. I'll drive it a few more times to see if I can get a little more information. Before starting this project, I purchased a transmission adapter for my jack. This really makes removing and installing the transmission relatively easy. I'm finding the hardest part is getting the four screws holding the drive shaft to the differential the hardest part. I gave up on using a torque wrench and had to borrow a crowfoot wrench to get to the differential side of the coupling. Does anyone have a suggestion?
-
wide ratio FS5W71B slipping out of 3rd & 4th
Zed Head I just found this in my search: It agrees with your thoughts on the root cause of the noise. I have to admit that I dropped the transmission onto a rubber mat when I was trying to fit it into my vice. If it landed on the countershaft, that could of damaged the bearing.
-
wide ratio FS5W71B slipping out of 3rd & 4th
Good point on the countershaft. I didn't know 4th was a direct drive. If it's an issue with one of the three countershaft bearings, is there a way to test them? They were all replaced so they should be fine but I installed and removed parts so often to fix errors, maybe I damaged one. Other than that should I check to see if gears are not properly matching? One issue I had with the countershaft was that I was unable to remove the countershaft drive gear. This required that I remove both the main and countershaft at the same time. After its removal, I tried a gear puller and an ultrasonic cleaner, but it wouldn't budge. I wonder if I moved the drive gear outward a little on the countershaft. There is a potential that I mixed up a couple of gears between the 3 transmissions I had open although I tried to keep them separate. The tooth count on the shafts are as follows from front to back: Main shaft 22, 28, 28, 33, [adapter plate], 36, and 19 Countershaft 29, 27, 19, 14, [adapter plate], 23, and 31
-
wide ratio FS5W71B slipping out of 3rd & 4th
I installed the transmission and give it a try. I'm getting a bit of whine; however when I let the clutch out, even in neutral. For some reason, no whine in 4th gear but it reappears in 5th. I checked the fluid level and it is up to the fill hole. Gears 1-4 are out of a 4-speed transmission. transmission.mp4 I might of put the wrong throw-out bearing (I had 2 different ones sitting out) in since the noise is only present when the clutch is out. Any suggestions? The attached video has the whine.
-
Zx 5 speed rebuild
I use https://smallpdf.com/unlock-pdf
-
wide ratio FS5W71B slipping out of 3rd & 4th
EuroDat, I think you spotted the problem. I took a few measurements and couldn't see how the countershaft would NOT fit so I was wondering about the input shaft. Nissan must of put the kerf in the input shaft where they did just to see what fool they could fool. Thanks all for your help. Jeff
-
wide ratio FS5W71B slipping out of 3rd & 4th
I'm not feeling a gap under the cover. I'm using a paper gasket without sealer. After disassembly again, and bumping the counter shaft in with a dead blow hammer, I got the following measurements of the protrusion of the bearings beyond the casting surface: Before hammering the difference between the protrusion of the main and countershaft bearings was 0.04 inches After hammering the difference between the protrusion of the main and countershaft bearings was 0.13 inches This extra 0.09 inches seemed to have helped although I'm feeling some resistance when I turn the input shaft by hand. I'm assuming I must use a countershaft shim. Is that correct? Should I use a fresh gasket maybe of thicker material to compensate for compression?