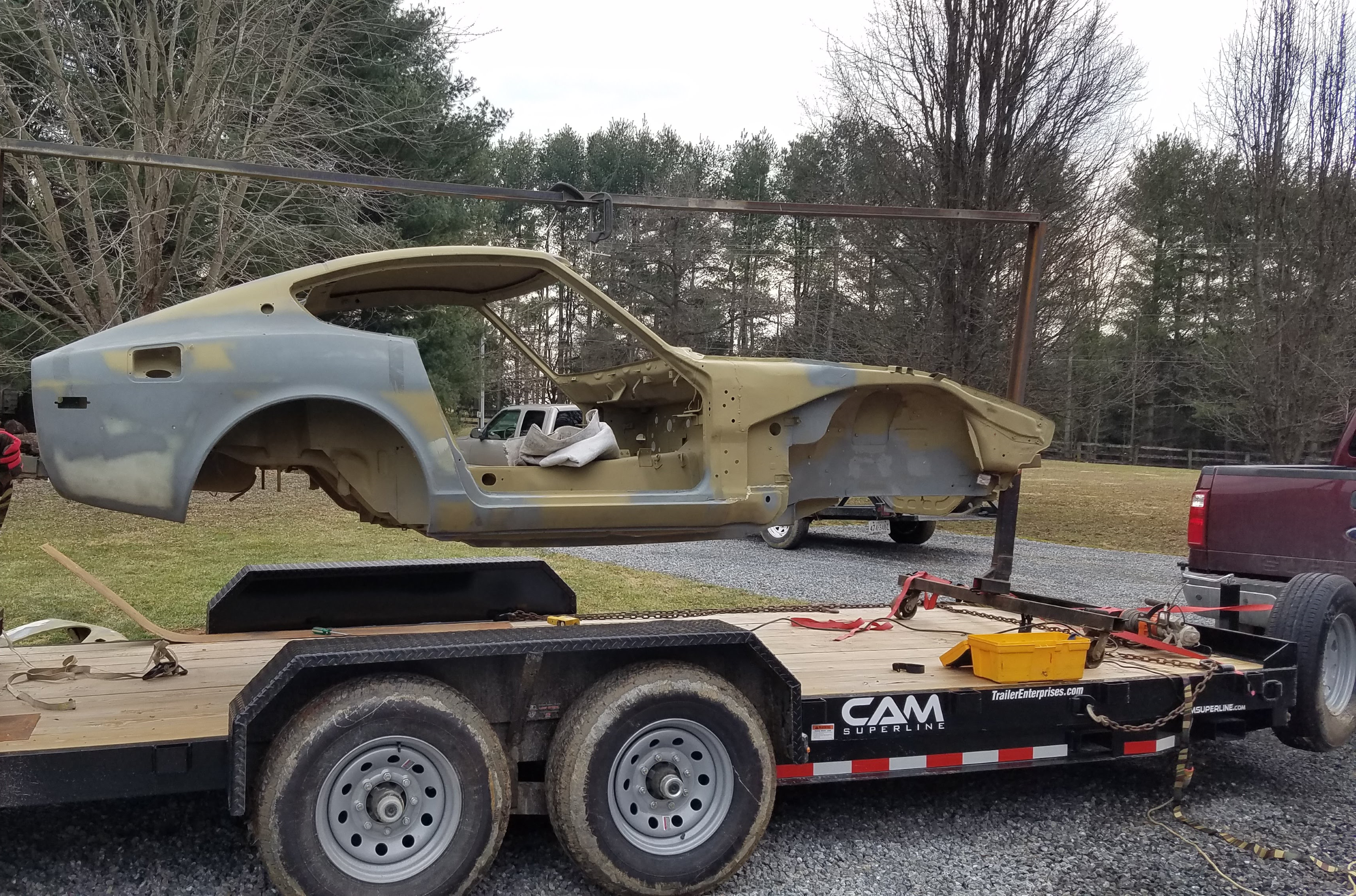
Everything posted by ETI4K
-
Perplexing "FUEL" light malfunction
Absolutely!
-
Perplexing "FUEL" light malfunction
Yep, had my chance and I blew it. So, arc suppression diodes all around! Did you see the Combination switch teardown info I posted in Knowledge Base Electrical. Good pics of eroded contacts. Sorry for off topic commentary ?
-
Perplexing "FUEL" light malfunction
As an aside, does anyone know how current production vehicles trigger a low fuel warning? Perhaps this is an area where a leap forward would be of value.
-
Rear control arm bush alignment
I am always averse to changing an engineer's decision unless I know everything that went into the taking of that decision. The problem is usually understanding all the loads and in this case, knowing how the spindle was specified, metallurgically. If one were to remove the head and threaded end of the 5/8 bolt, they'd have a pin. Could be a pin for a shear application, as most pins are. It's fair to say, I think, that the failure mode for the spindle pin would be a double shear, or maybe a single shear with a moment. Exactly the kind of loads pins are made for. You can select the grade of that bolt/pin, 3, 5, 8, etc., and if you know the strength of the spindle pin, can do so to match. Other than that you have to rely on anecdotal evidence, and the problem with that is you never know all the facts such as static loads, impact forces, installation details, etc. that the part has experienced. My favorite example. Please bear with me a moment: We used to ship very expensive equipment upright, which meant it had to go by 747 freighter, which was expensive. Manufacturing wanted to ship it on its back, something it was never designed for. So one day they laid one on its back and shipped it somewhere and back again. It came back fine (looking) and so they declared the equipment could now be shipped flat, since they'd proven it worked. Scary. I believe we've all done things where we thought this will probably work, and it did! Does that mean it's a good idea? You'll never know. All you can say is, "Well, it hasn't failed yet." Purely for the fun of it, I am making new pins on the lathe. I too will be holding my breath for the first few miles. ?
-
The blue 510
That does not look like it feels good. Sorry that happened to you, though the thread looks nice in your hand. Do the sewing yourself? Last time I pulled a stunt like that, my best buddy sewed me up. Saved me a lot of trouble and cash! Now I owe him.? Funny, your story reminds when I was in high school, I tried to use a similar wire wheel to clean up a metal vacuum line. Within 3 seconds of starting, it was ripped from hand and I never saw it again. Ahh, such good memories!
-
Restoration of BringaTrailer 240z - HLS30-35883
I have a brand new factory fender and hood, still in the boxes (bought in 2003). They're for a 280. I'll get them out and shoot some detailed pics of the body lines, if that'd be helpful.
-
Repro 240Z Fuel Tank Coming Available
Was that tank holding fuel by virtue of undercoating?
- 1976 280Z Restoration Project
-
1976 280Z Restoration Project
I really admire the extent to which you've persisted, not with the restoration, but the documentation thereof. I've never been able to force myself to stop working, clean my hands, find the phone, and snap a few. My hat's off to you. I especially appreciate your commitment because your car and mine are very nearly identical in condition (when you started), and this thread has already been of great assistance, though I haven't "officially " started quite yet. Saturday will be a great day.
-
Trip stats, gas milage, oil consumpion, operating temps.
I used to drive an old 911 that, according to the technical specifications, would consume about 1 quart per 500 miles. Aftet reworking the motor, yep, it used 1 quart about every 500 miles. The car was so fun to drive though, I didn't care. I also didn't ever compute fuel economy, which I would always do as a mental exercise after leaving the pumps. I just didn't want to ruin my fun by knowing how bad it was. ? The info you've posted will serve as a great point of reference for monitoring engine condition.
-
Air Compressor for Blast Cabinet
Time is money as they say. A friend completely sand blasted a Triumph TR6 he was restoring - frame, body panels, suspension, etc. Used a Craftsman siphon blaster ($20 iirc) and a compressor similar to the one Bill is considering. Laid out a very large tarp to catch the sand so he could recycle it. It took forever, but he got it done. So, if you want your time back, you have to spend money and go with better and bigger equipment. Deals can be as had. I paid $650 for my compressor (one year old) with a line drier and supplied-air respirator pump, lines, and hoods. Came from a bedliner company going out of business. They were SO relieved someone wanted it! I was happy to oblige. ? The A/C condenser and furnace blower is a great idea for getting water out of the air. A long time ago I ran 1" copper pipe all the way around my garage with one drop leg. Drain valve at the bottom of the leg and the air take-off was 12" higher. It worked pretty well, but as with all things, it becomes a matter of degree. Anything is better than nothing, and more is better still.
-
Air Compressor for Blast Cabinet
FWIW, I get 35CFM at 175psi from my compressor (twin 5HP pumps on a 120 gallon tank) and there are still times when certain media just won't flow well and it seems to take forever to get parts cleaned. It seems the media tends to fill the hose and then the suction force can't lift it to the gun because there's no air flow for transport. The best performance seems to come by using dry air (ideally through a refrigerated line drier), and low density media like medium or fine crushed glass. Coal slag doesn't flow quite as well, but it's cheap and everyone sells it. I've used a mineral (can't recall name) that is mined in Canada that is VERY dense and can be recycled dozens of times. It's great, but again has a hard time getting to the gun. That said, if you really want to see some parts get cleaned quickly, use a pressure blaster or a water siphon blaster (no air required). You can use Hold-tite 102 to run with the water to prevent flash rusting. The problem with either is it's tough to recycle the media so you will most likely run through it.
-
Staked Nut and Steering Gear
Here's a source for rebuilt racks.. They also have new ones for the 280s. https://www.buyautoparts.com/buynow/1971/Nissan/240Z/Rack_and_Pinion/80-70090_R
-
Crank snout turning nut
I think Patcon has potentially scaled the problem quite well with the pic of the blown hub. A few (okay, maybe a lot of) assumptions here, but I might guess you maybe had most of your weight on the end of that pipe. Let's assume you weigh about what I do, 170lb. You were applying about 850 ft.lbs. of torque to that hub (if it wasn't already cracked as you suggested). Further, if all six pistons are stuck "equally well" you're having to overcome the binding of six pistons all at once by turning the crank. Perhaps the way to go at might be to start as Captain suggested, remove the crank and drive the pistons down; and rather than use a hammer, why not a hydraulic press using very slow and steady pressure?
-
Crank snout turning nut
If those calipers are still handy, would you mind measuring the damper hub OD?
-
Crank snout turning nut
I'm running Inventor 2020. If I'm making anything at all, I'll create the models first. I have found my productivity is significantly greater as opposed to figuring it out as I go. Also, my material waste due to errors and rework time dropped to near zero. Mostly, its benefit, as I'm sure you know, is as a design checking tool. If there's something your working on and need to "see" it in 3D, I'm happy to help (I think! ?). PM me.
-
Crank snout turning nut
Would it be any easier to make it this way? The inner and outer sleeves would have to be welded (plug weld through the flats), but it might obviate using a broach or a shaper. Since I have neither, I'd have to make it something like this. The inner sleeve could be turned to a thickness of .125 to clear the key.
-
Crank snout turning nut
CO: Are you cutting the keyway with a broach?
-
ring gap posistion
My motto has always been "If you're not bleeding at the end of the day, then you probably weren't working." This may explain the countless scars...
-
ring gap posistion
I would use the Total Seal rings again just for the clean oil aspect, if that's all they were good for. Also, if the rings do in fact rotate, and if they don't rotate in sync with each other, one could argue the ring gaps may well line up at some point allowing combustion gases a clear shot to the crankcase. I would love to see real numbers on performance benefits of reducing blow-by, excluding the supposed benefits of not coating intake runners with oil, etc. Where these rings would really be of value might be in a diesel engine. I swear the oil in my truck turns black in a hundred miles (WAG, but you get my point). I can't believe all that carbon is good for the engine, yet they can run over a half-million miles without a lot of trouble.
-
ring gap posistion
I owned a water buffalo for several years. Rode year round, in the rain, sun, cold, whatever. Loved every second of it. Thanks for the posting the pic. I hadn't thought about that bike in a long time! Sorry, if I am extending the off-post commentary. As I've said before, I get easily distracted. especially by fun stuff.
-
ring gap posistion
CO: There were so many issues affecting my engine's performance back then (such as an undersized exhaust, all stock emissions controls, questionable injectors, etc.) that when I changed over from TS rings to standard design types, I couldn't really tell a major difference at the ball of my foot. That said, I was astonished when I did my first 3K mile oil change with conventional rings. With the TS rings, the oil was CLEAN! Conventional rings, not close. Anyway, THIS build gets TS rings again. BTW, I'm not embarrassed to admit I can fall for the placebo effect. "Oohh yeahh, those gapless rings are the *hit. I bet I got another 20HP!!". Tongue planted firmly in cheek...
-
ring gap posistion
Another solution to the ring gap spacing issue would be to use Total Seal's Gapless Rings. I ran these (perhaps an earlier version) after my initial engine build in '94. I still staggered the gaps, though not necessary for compression leakage issues.
-
Current Load Calculations - Much larger alternator needed
I have changed my mind several times about how to proceed with my wiring changes. My goal, of course, is to improve reliability and performance, i.e. reducing IR losses. Further, I want to make troubleshooting faults quick and easy. So AK, I'm with you on number 4 - reduce current loads on the fuse box. I arbitrarily selected 10A as the threshold for switching the load over to a new discrete relay with its own new (different) fuse. In addition, I am replacing all oem relays with new Bosch style units. That's not much trouble, but I've also decided to fuse protect the control signal (to the coil). Just a bit silly, I know, but if ANYTHING quits working, getting it sorted should be a breeze. Also, as you know, I am colocating ALL relays and new fuses. At some point I suppose the question becomes why not completely eliminate the oem fuse block? That's just one point of my vacillation.
- Current Load Calculations - Much larger alternator needed