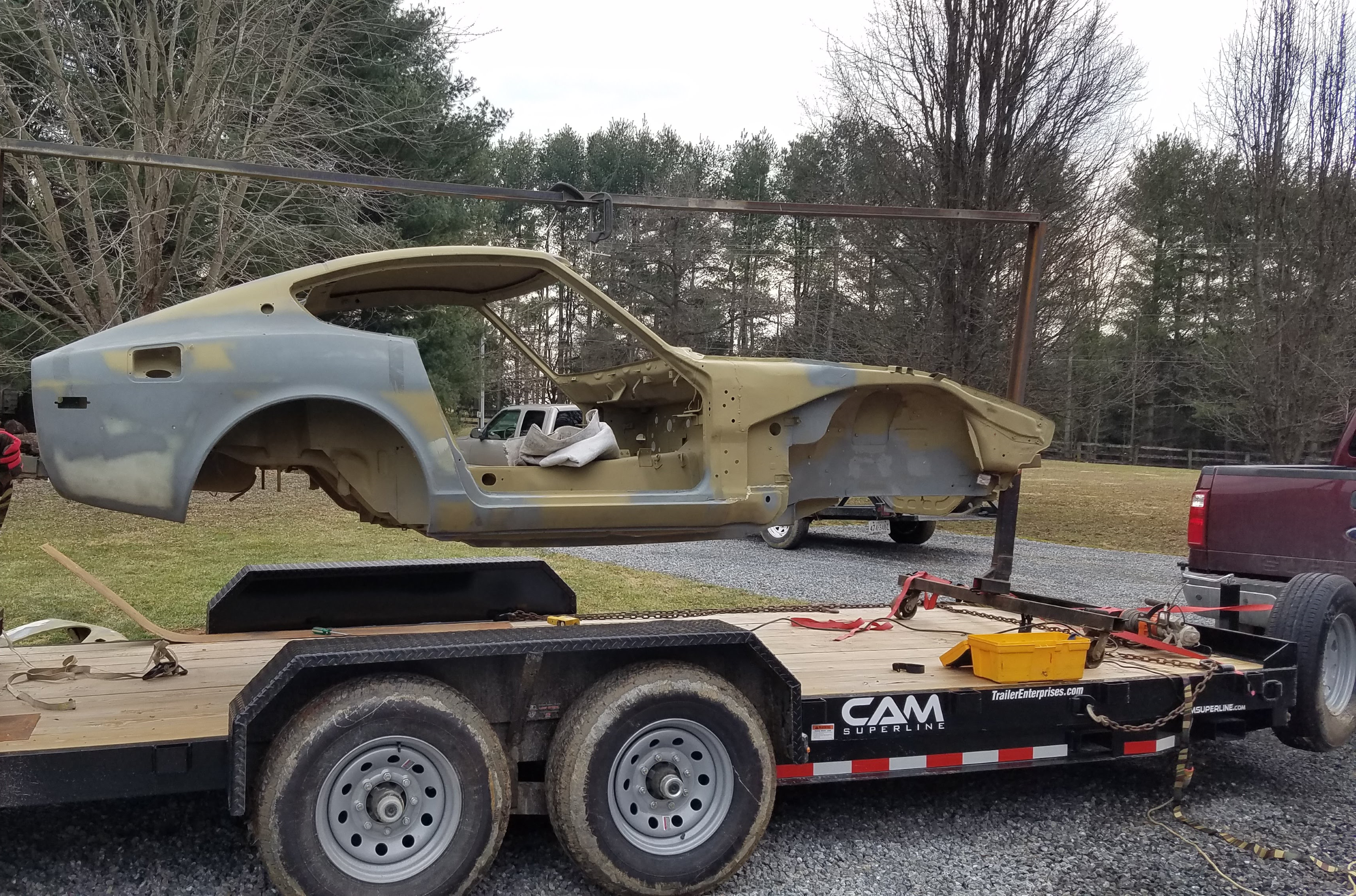
Everything posted by ETI4K
-
Quartz clock hands removal
Alternatively, you can use a piece of cardboard to protect the face. Cut a slit in the cardboard and slide it up to the stem. It will fully cover the face. Then use a fork to gently pry upward on the needle, as @zclock suggests rocking it back and forth. The fork applies force to the needle that is not axial to the stem so it is possible to slightly bend the head of the needle, so be gentle. If the angle of the fork to the needle is too large, just use a spacer under the fork to direct the force more in line with the stem. EDIT Sorry, kept writing needle, meant hands.
-
Gas Tank restore and POR15
What would be the problem with missing one or two nuts/bolts, anyhow?
-
New clutch...Noise when clutch is not depressed and trans in N?
FM - Frickin magic
-
New clutch...Noise when clutch is not depressed and trans in N?
Hmm, interesting. I know the friction modifiers work well for their intended purpose, especially when the machine was designed for their specific use. If used in a trans (I'm guessing that was not originally designed for it), would their be a chance that, for example, the synchro rings would become "too slippery" and you could get the grind back?
-
New clutch...Noise when clutch is not depressed and trans in N?
Yeah, I'm with you completely. Valve train sounds (aot noise) have always bugged me, other not so much. A good stereo drowning out those annoyances isn't masking, it's enhancing the user experience.
-
New clutch...Noise when clutch is not depressed and trans in N?
What was the most commonly reported need for the rebuild(s)? Were you ever able to do a before and after comparison?
-
New clutch...Noise when clutch is not depressed and trans in N?
Thanks for the insight. What we need is a way to test a bearing that's better than the give it a quick flick and listen test, or spin it to feel for roughness. These techniques work fairly well after you've gotten some experience, but it's not a reliable method, especially since you can't vary the load. As you mentioned, there are several bearings operating, and any one or more could combine to sing under certain conditions. Of course, there's always the shotgun approach - change 'em all!
-
New clutch...Noise when clutch is not depressed and trans in N?
DavidF: That's the part I'm having trouble with. If the pressure plate and release bearing are lightly loaded, the noise stops. I am assuming "slightly" doesn't begin to release the clutch. If I'm wrong, skip the rest ? So the clutch disc is still coupled to the flywheel and spinning at engine rpm. The release bearing is now spinning at or near engine rpm. The torque on the transmission input shaft, if any, hasn't changed and neither has its rpm. The crankshaft has some axial reaction force loading it toward the front of the motor. The clutch release lever is loaded to eliminate any free play. I think that's everything that's going on. What of these, or others missed, acts on the input shaft bearing to change its loading? Before I start assembling my car, I plan to rebuild the trans (same one as yours David F) and it'll get new bearings, but I'd really like to know if maybe something else is also contributing to the noise problem so I can fix it now.
-
New clutch...Noise when clutch is not depressed and trans in N?
site: I think we're all with you!
-
New clutch...Noise when clutch is not depressed and trans in N?
It's quite odd that, presumably, the sound was not present before the new bits went in. There's no chance it's clutch misalignment. The disc is the only component that could be misaligned, and if it were, you'd never get the trans back in. And even if you were to get the trans reinstalled with a misaligned disc, as soon as you depressed the clutch pedal, the disc would be freed to center itself. Noises are the hardest to describe. If the release bearing were in light contact with the pressure plate, it would be making some sound - audible or otherwise. Depressing the clutch would load the bearing past its light load, incidental contact condition and either make it sing or reduce its sound level. Try readjusting the throw on the master cylinder to ensure ample clearance (free-play) in the pedal. It is possible that the parts you received are not correct (can you say misboxed?). It's happened to me. Are you certain the clutch release lever is properly seated on the pivot post, and the lever has freedom to move? Be certain there's no residual pressure on the clutch slave. Cracking the bleeder will let you know - if brake fluid blows out, not passively drips out, then you had some force acting on the release lever. Well that's it. I'm in the middle of cocktail hour!??
-
S30 Half-shaft Disassembly and Rebuild
Got it. When that thing broke free, I'd thought a bomb went off. Pretty sure I had just about all the press was worth on it - 20 tons. In one instant it shot the bottom cup completely free and the top one as far as it could move. Done lots of u-joints and never saw one break free like that. Nice impression from the cup. Oh yeah, 11mm is confirmed.
-
S30 Half-shaft Disassembly and Rebuild
So much for plans to measure the bearing diameter. I could not (cannot) break down the half shaft bc the u-joint won't cooperate. Left it overnight with WD to soak and kept about 10(?) tons of force applied. This morning - cups still will not move. Can anyone confirm the flange is forged? Really looking forward to NOT breaking it. Yep, retaining clips are off both cups, and the socket is large enough. I shall press on ?
- S30 Half-shaft Disassembly and Rebuild
- Current Load Calculations - Much larger alternator needed
- S30 Half-shaft Disassembly and Rebuild
- S30 Half-shaft Disassembly and Rebuild
-
Current Load Calculations - Much larger alternator needed
Measured pics would be great - thank you for offering to do that. A hinged drop-down assembly with lighting is also interesting. I'd probably implement that so the LED lighted automatically whenever the assembly was in the down position. ? Lots of fun options. The more I get into this, the more I am leaning toward the smaller footprint solutions. I am up to 25 additional fuses and 13 relays (some are replacements for OEM relays). Thanks for the link. Back to searching...and searching... and.....
-
Current Load Calculations - Much larger alternator needed
It might. I will need four boxes that are about 3 x 4 each plus one box for the relays that will be about 4 x 9. It's a lot of real estate. I started off planning to buy the fuse panels and making the relay box using typical Bosch style relays bc they are ubiquitous and cheap. Then I found the mini(?) or micro(?) relays made to plug into fuse boxes - they are a lot smaller. Searching for these parts could be a full-time job for the hours needed to find the right bits. I couldn't imagine doing the searches if we weren't in lockdown. Every night and weekend would be fully consumed. Since I will be removing some old relays from under the dash, there may be room in that area, but I am sort of expecting there won't. The problem is my car is 100% disassembled so I can't fit check anything, but I know the space under the seat works. I kinda like the idea of a pull-out panel, not so keen on flipping the seat up.
-
Current Load Calculations - Much larger alternator needed
Wheee! - Thanks for the details needed for modifying the bracket. That'll make the job much easier! btw: Very nice pics above. I'm up to page 73 of your thread! AK - Yep, good advice. Planning to make dramatic changes to the entire harness while it's out. First will be wire gauge upgrades where needed. I'm actually working right now on a wiring diagram to add features (low oil level, low coolant level, additional sensor wiring for MegaSquirt, electric power steering, carjack shutdown, taking all high loads off stock switches and running them through relays, etc., etc. I'm adding fuses for the loads as well as the relay coils, and replacing the fusible links with circuit breakers. I figure if something shuts down on some cold night while it's pouring down rain, all I have to do is find which discrete circuit is the problem. It means I'm adding a lot of fuses, which I plan to locate under the passenger seat. That of course means I need to be able to easily move the fuse panels or seat so I can service them. Haven't decided to make them slide out from under the seat or hinge the seat out of the way. Either way, I'm fabbing new parts
- Current Load Calculations - Much larger alternator needed
-
Current Load Calculations - Much larger alternator needed
Zed, Just finished reading the articles. The boat article is a good overview of case sizes and styles as well as illustrating your point. I've been on the MAD site before (very good information there), but I must be missing something on the Mazda article, except of course that a new MX-5 would be even more fun than my wife's current one. As an aside, I've owned a lot of different cars, Zs, Porches, Jag, Hondas, Ford, etc. On a dollar per smile basis, I swear that Miata PHT wins. The PHT is key! Back to alternators. In summary, perhaps we can say at idle, if your load is very high, as in my table at the top of this thread, you'll be pulling on your battery. Coming up on RPM, if the alternator output is greater than the load, the battery gets recharged and the alternator takes over supplying the load. If the alternator doesn't have it, the condition of your battery will be determined by how long you use circuits that extend the load past the alt's output, and are you driving long enough to "refill" your battery. It's a multivariable equation. The easiest path to follow then is probably to rely on anecdotal evidence or use the ever popular overkill method. As for me, my problem may have been solved. My brother offered to give me a spare (12si) 140A alternator he has on hand for his Cadillac. It's free and free wins. If it won't keep up, there's plenty of options in the 12si family that will. This is another good bit of info - taken from the Mazda 6 Club site and has to do with installing a 260A alternator: https://www.mazda6club.com/threads/new-high-output-alternator-solution-for-us.235352/ At 140A, I might get by on #4, but I plan to run #2. Later in the thread someone recommends Knu Flex wire as being very easy to route, which is exactly what I was looking for.
-
Current Load Calculations - Much larger alternator needed
Also, another issue to deal with is output at idle. I can use a smaller alt drive pulley, but the rpm ratings for ones I've looked at are typically 6k. I plan to be able to run to 7k. So if I use a smaller alt drive pulley, then the real rpm max will be less than 6k. So you end up having to use a much larger alt (output) just to get the current you need from idle up to the rpm limit of the alt.
-
Current Load Calculations - Much larger alternator needed
I seriously wanted to convert to serpentine style drive. The BHJ Dynamics damper and Sanden A/C compressor are available in 8-rib, and of course, an alternator pulley is no problem. The problems are, I couldn't find a water pump pulley, and to use a single belt (with A/C) requires two idlers. Fitting them in (in CAD) was not easy. Thanks for the article link. I'll read it later.
-
Current Load Calculations - Much larger alternator needed
I've been looking at the 12si for a while. They can pack a lot of amps into one, which at 140A or better makes me nervous about reliability. Also was looking at the CS144 which supposedly can better handle higher outputs, but they tend to be a bit pricey. Before I had decided, my brother offered me a spare he has for his Cadillac. It has a 140A capability, PLUS IT'S FREE. Guess my decision is taken. It'll be easy enough to upgrade later if it can't keep up. Thanks for the link.
- Current Load Calculations - Much larger alternator needed